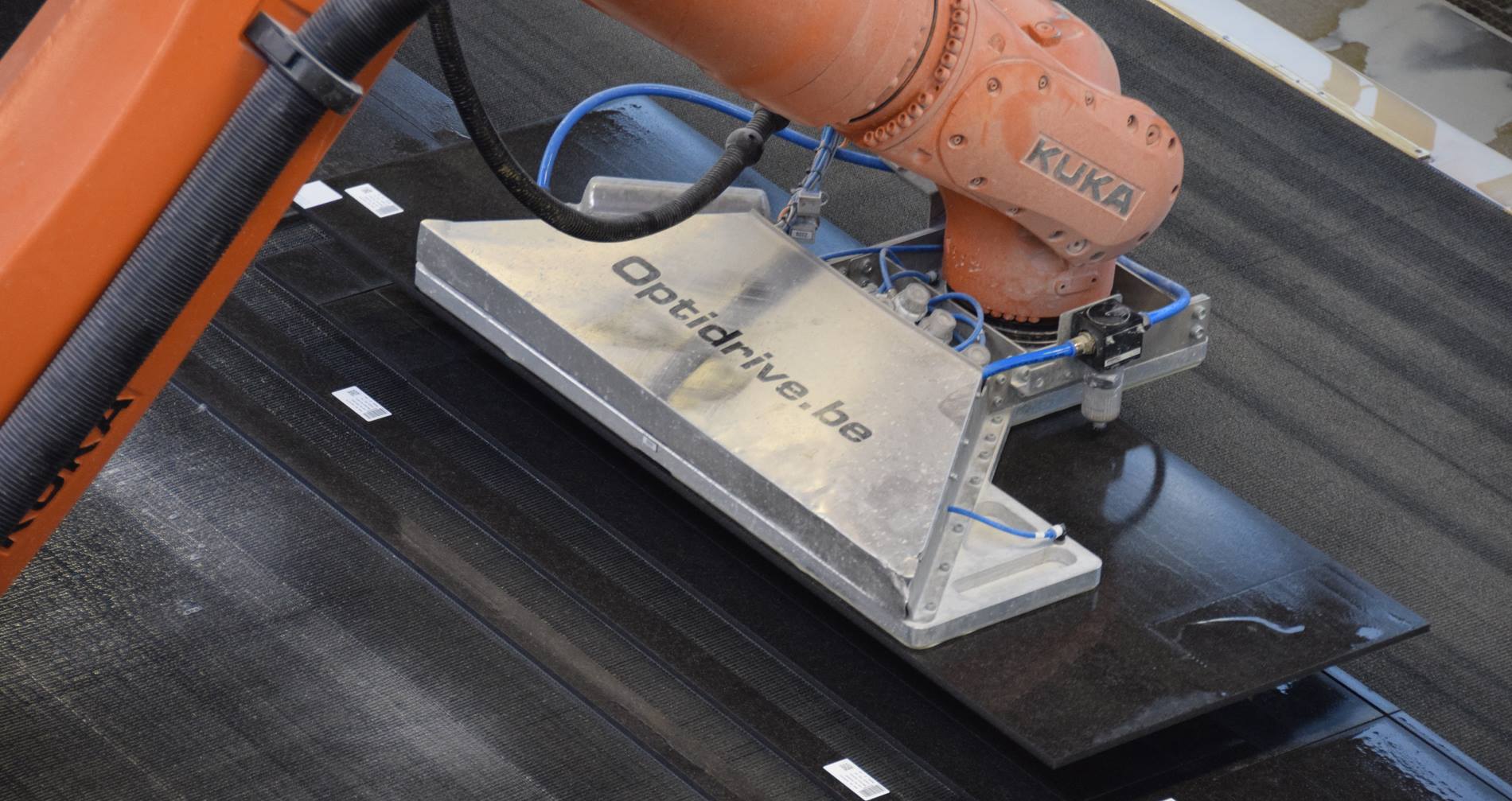
Optidrive and Erbi: Strong partners in production
Official KUKA System Partner Optidrive has developed an automation solution for the Dutch manufacturer of kitchen trays Erbi where 2 KUKA robots are used in production.
The demand for their kitchen counters continues to rise and, in order to continue to anticipate on this, Erbi felt compelled to automate its production processes. The company Optidrive, located in Leuven, soon came into their sights as the specialist in the field of grinding and polishing. Optidrive supplies robotic installations for automated grinding, polishing or deburring in the metal, plastic or stone industry. Therefore it was absolutely clear to Erbi that Optdrive was the perfect partner to collaborate with. Raf Dequeker, General Manager of Optidrive, developed two automation solutions for Erbi.
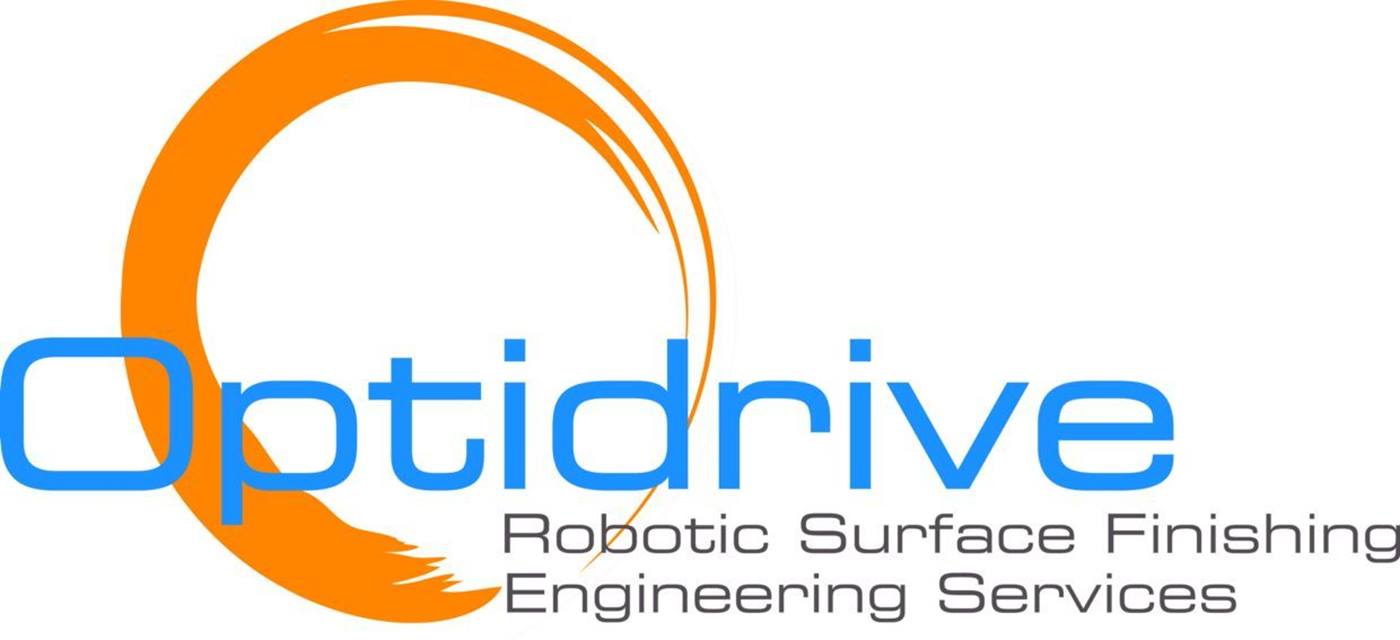
Two material handling applications as solution
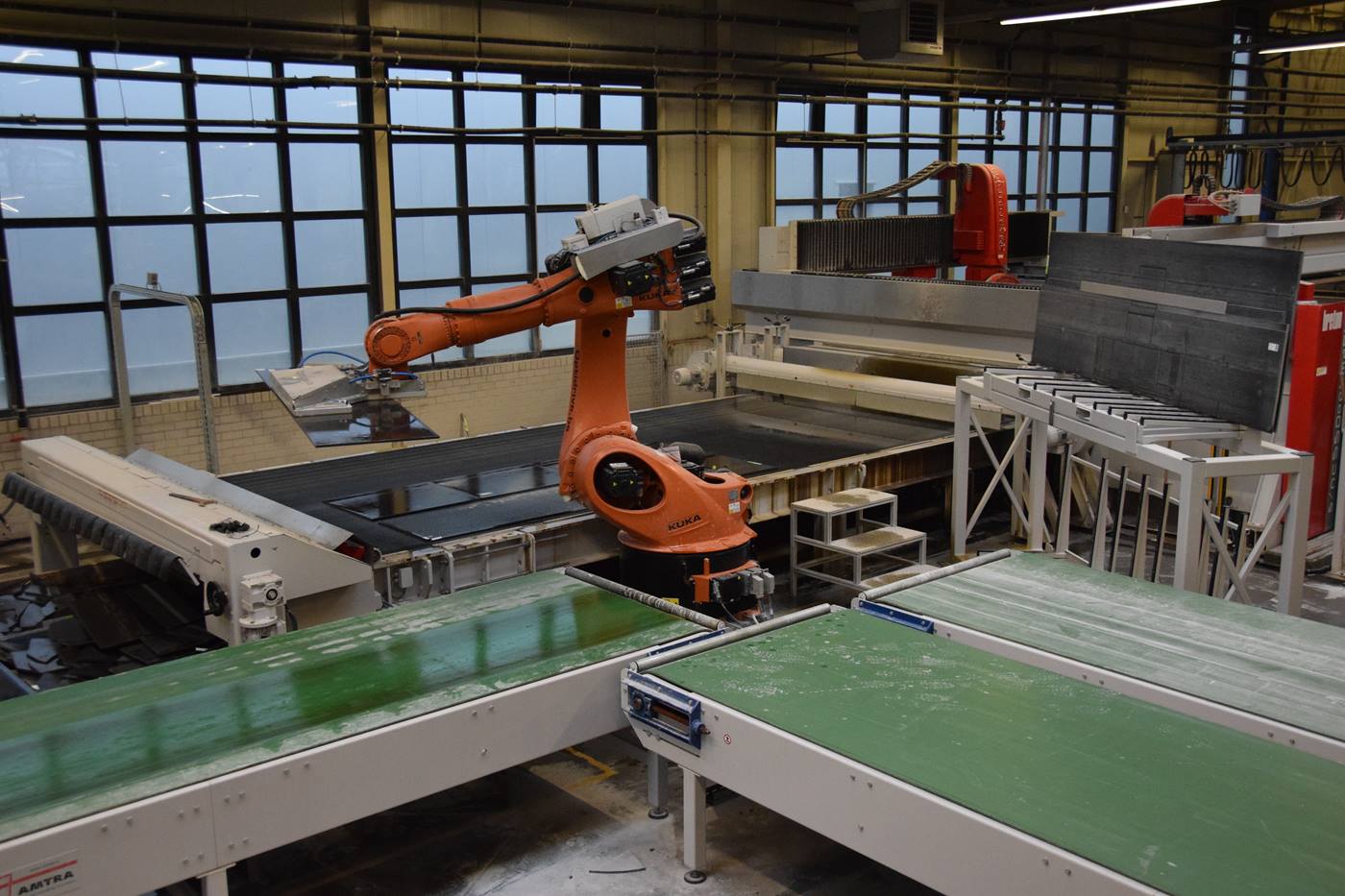
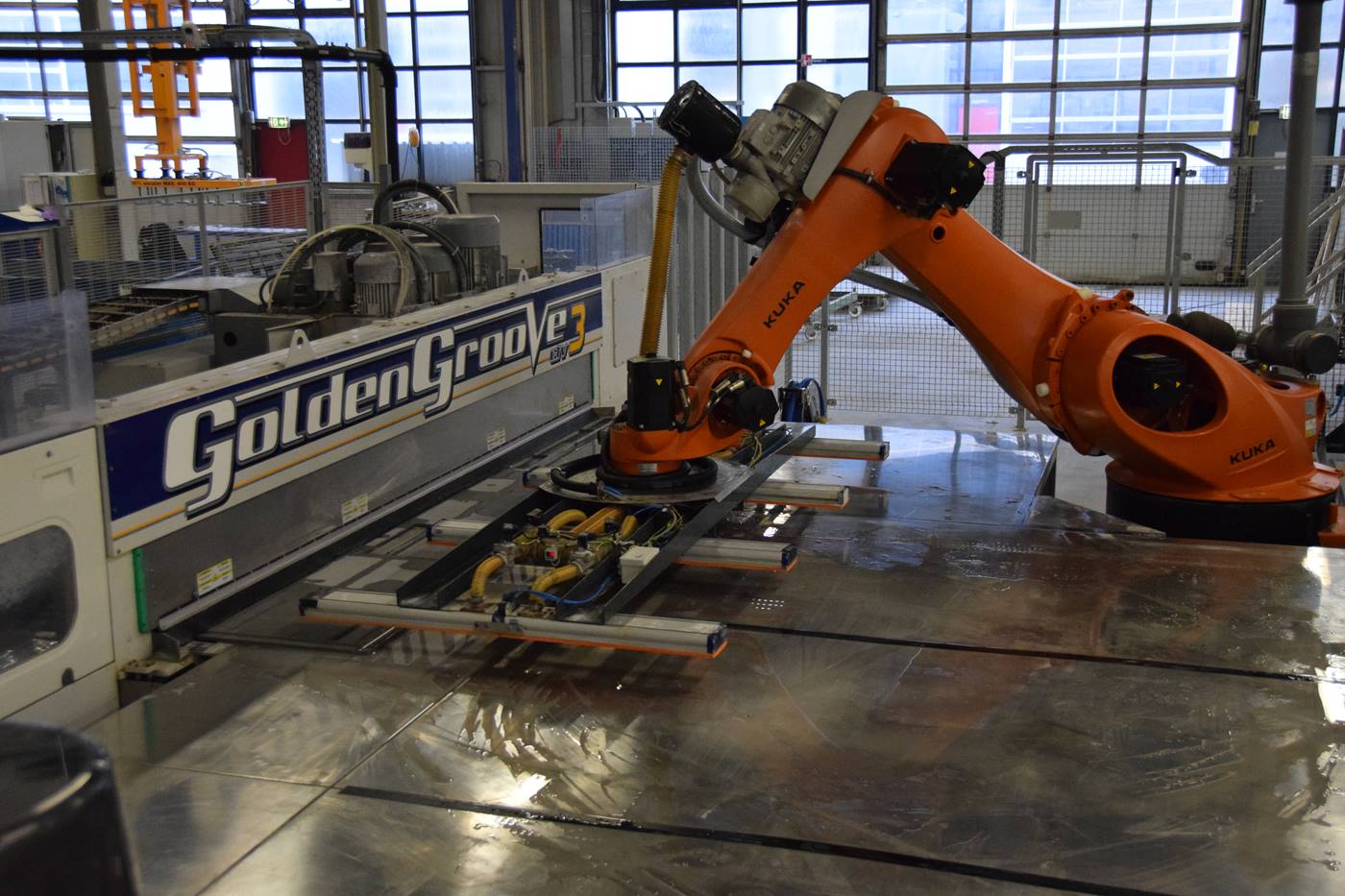
Without this automation solution, we would never have been able to respond so efficiently to the increasing demand.
A productive cooperation
