
Safe food production with Hygienic Oil Robots
Sensitive industries such as pharmaceuticals and food require technologies that do not compromise on hygienic handling – and ensure that products are safe and edible. KUKA has launched a complete HO portfolio whose robots meet these high requirements.
Tiempo de lectura: 3 minutos
One in eight food products is contaminated with mineral oil residues that can be harmful to health. Some of the dangerous contaminations happen in the automated production and packaging process, but they can be completely prevented with the right technology. This is where KUKA's Hygienic Oil (HO) portfolio comes into play.

For machines used in these industries, this means that they must be designed and built in a way that operating fluids – including lubricants – that are hazardous to health cannot come into contact with food products. If some lubricant does escape unplanned, it must not endanger health or impact taste. “As KUKA, we take this very seriously, especially since our robots are increasingly being used in these areas,” explains Dieter Rothenfußer, portfolio manager at KUKA. “All axes of our HO robots are therefore equipped with food-grade lubricants, as is the energy supply system to the robot tool.”
Equipped with food grade lubricants
The so-called NSF-H1 lubrication is suitable for foodproducts. This means that if a lubricant from an HO robot comes into contact with food – for example, in the event of a robot malfunction or if oil vapors escape from the machine due to compressed air – this is harmless to consumers. In addition, the machines are designed, built and installed to prevent the ingress of operating fluids such as lubricants, hydraulic fluids and signal-transmitting fluids into the product.

New robot variant completes HO portfolio
The range of hygienic oil robots from KUKA is now complete: three hygienic variants of the KR IONTEC have been launched on the market in 2023. They complete the portfolio, which previously consisted of corresponding variants of the KR QUANTEC, KR CYBERTECH, KR AGILUS and KR DELTA. “In cheese processing in particular, many of our customers have been waiting for this new robot variant,” reports Rothenfußer. The food industry has recognized the need for automation long ago. As early as 2021, the number of robots used in the food and beverage industry worldwide rose by 24 percent to around 15,300 systems. And the trend is continuing.

HO robots increasingly in demand in the food industry
HO robots, which are still relatively new, are currently mainly found where dry food or feedstuffs are processed, packaged, sorted or palletized. The KR CYBERTECH nano HO, for example, packs fresh bread in large bakeries, and the KR QUANTEC HO transports fruit and vegetable crates. The new KR IONTEC in the HO version is also already in use and is taking up its duties with more and more customers in the food industry.

Thanks to the expanded HO product line from KUKA, we can meet the needs of our customers in the food sector even better with our customized special machines.
Simple integration thanks to KUKA software
The new generation of KUKA.PalletTech palletizing software supports the KR IONTEC HO in this. It is particularly suitable for tasks in mono-palletizing, where it offers maximum efficiency with maximum flexibility. Whether single-pick and single-place or single-pick and multi-place: the software can be used to simplify a wide range of palletizing processes with all five- and six-axis robots from KUKA. Even without programming experience. The integrator helps with the selection and tailoring to the respective requirements. “Special solutions are often required. For these, there are so-called entry points where programmers can program the corresponding requirements in predefined lines of code,” explains Product Manager Michael Hohenäcker.

Requirements for hygiene, speed and flexibility met
When it comes to automation in sectors such as the food industry, software such as KUKA.PalletTech and food-grade oils are crucial success factors. They enable the requirements for hygiene, speed and flexibility to be met. Everything from a single source. Contaminated food can thus be completely avoided.
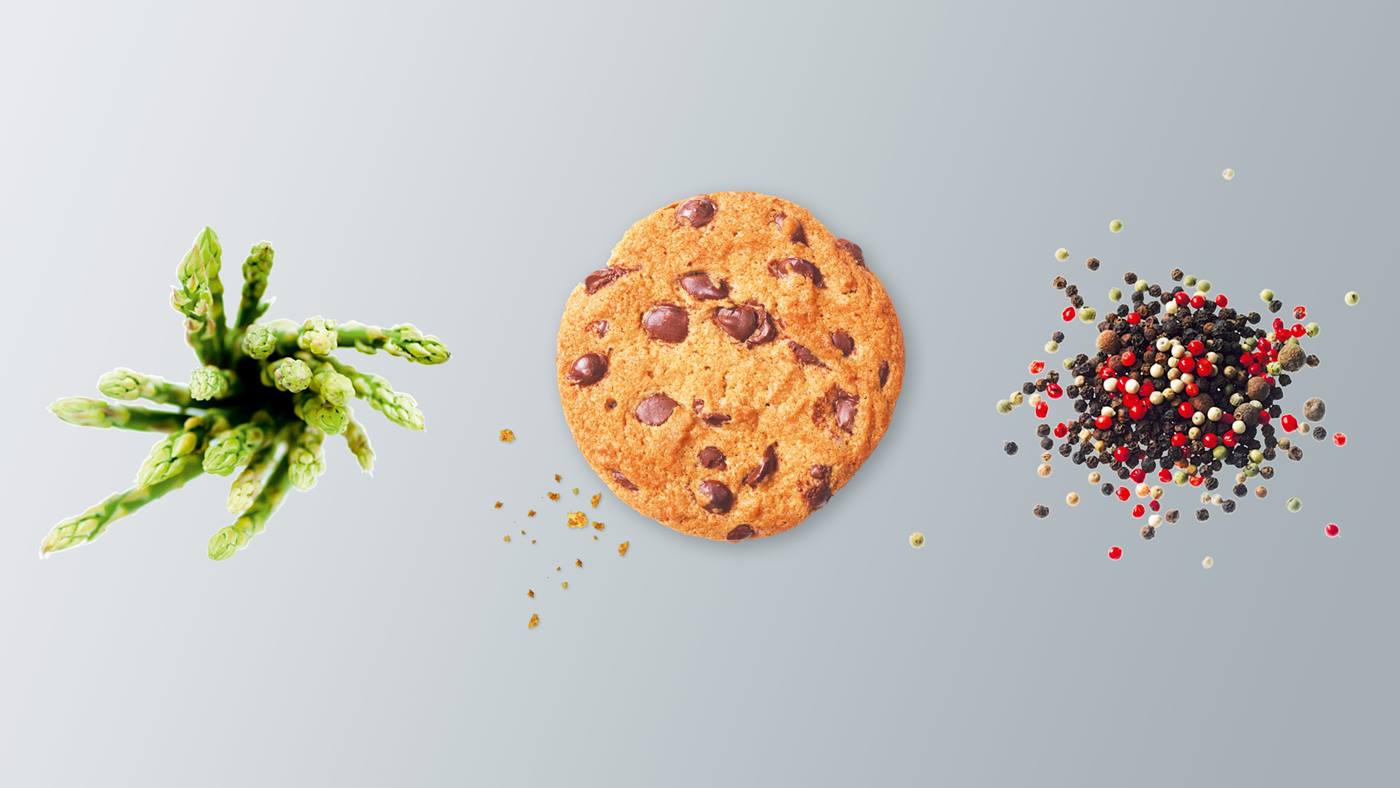
Siguiente artículo