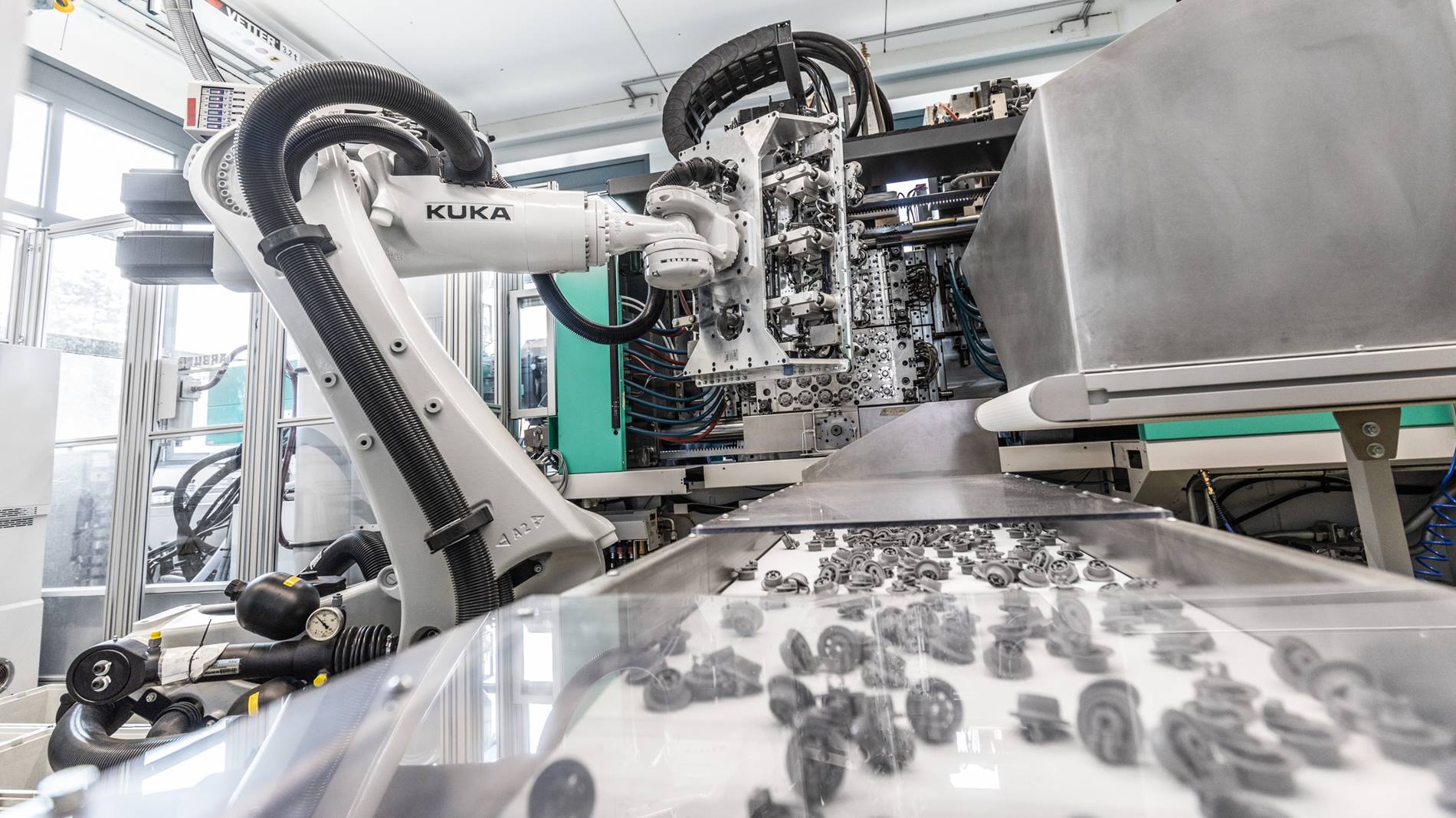
Success stories: How small and medium-sized enterprises benefit from their automation solutions
Many decision-makers in small and medium-sized enterprises (SMEs) still shy away from robots and automation. But those who try it often find it amazing how smoothly the integration runs and how quickly their investment pays off. This was also the case with the following SMEs, which give insights into their production.
Reading Time: 2 min.
The approximately 40 employees at Hermann Hauff GmbH & Co. KG in Southern Germany are happy about their higher production volumes and enormous efficiency in combination with the perfect utilization of their limited production space. Together with KUKA system partner robomotion, Hauff has completely automated the production of upper basket rollers for dishwashers. Since 2019, the six-axis KR QUANTEC has been working reliably, quickly and precisely with the Arburg Allrounder Cube 2900 injection molding machine, which integrates a reverse cube from Foboha.
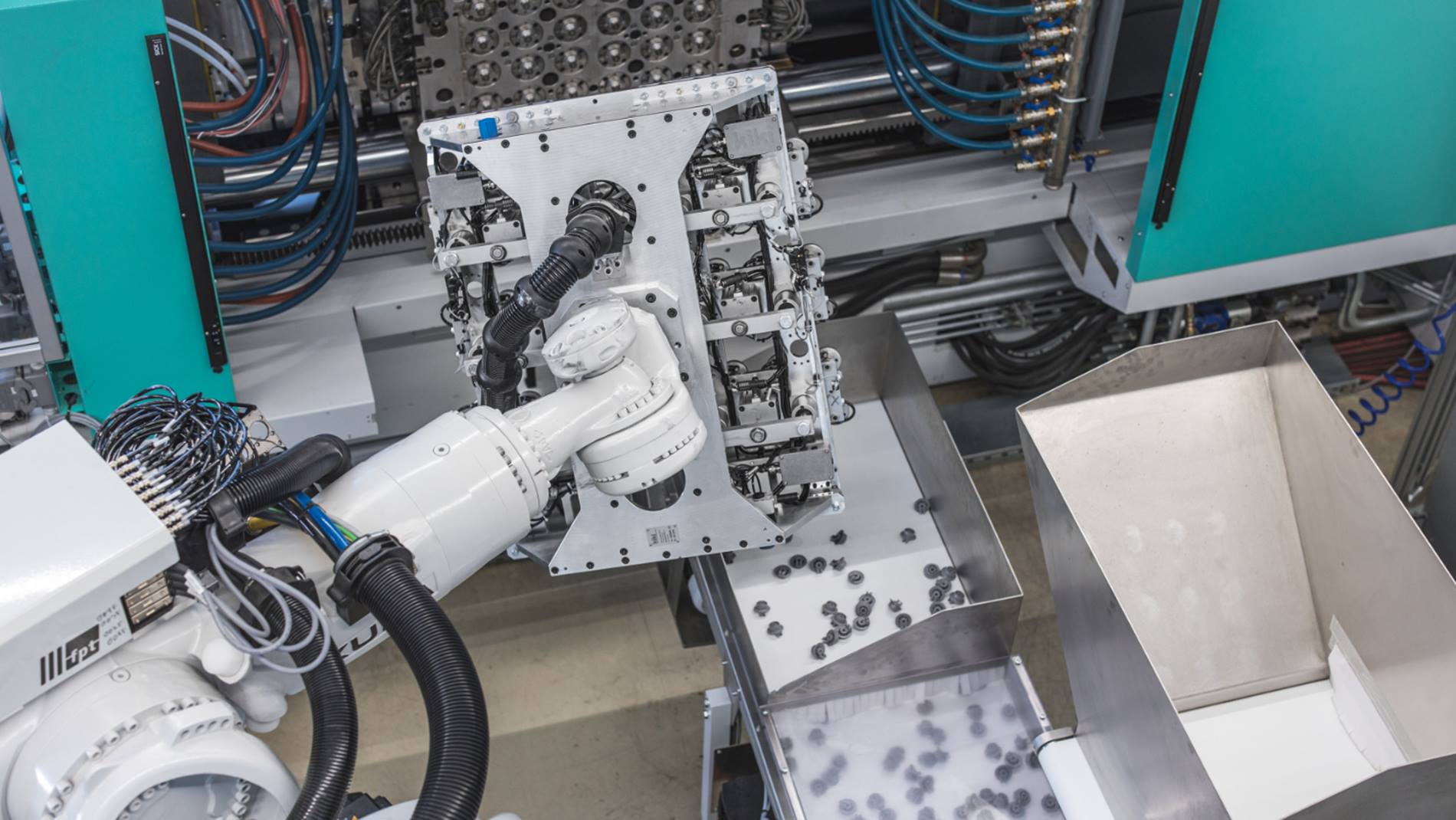
Palletizing robot assists with packaging
Simultaneously with the injection cycle, the robot removes the rolls from the lower part of the cube and inserts them into the sockets, later removing the finished plastic parts and depositing them on the conveyor belt in the direction of the packaging. In this way, 24 high-quality upper cage rolls are produced every 9.5 seconds. Additional support during packaging is provided by a palletizing robot from KUKA. The KR QUANTEC PA folds the shipping cartons and places them under the conveyor belt, where they are sealed after filling and stacked on a Euro pallet. In this way, three pallets – each containing 45 cartons and 70,200 plastic rolls – leave the company every day.
Employees are physically relieved
Hauff's management is particularly pleased with this solution, which saves space and helps the company to remain productive in times of a shortage of skilled workers. This is because the system runs independently, without any further supervision. After eight hours, an employee removes the fully loaded pallets from the system. The employees appreciate being relieved of physically demanding, monotonous tasks. And the company management is already thinking about further solutions with KUKA robots. Your way to the full success story and video.
2. Razor-sharp: Customized grinding and polishing
KR CYBERTECH industrial robots grind and polish the blades of Atlantic Chef kitchen knives at the Taiwanese company Liow-Shye. Thanks to the KUKA robots and their software, this works for different types of knives – whether for Western or Japanese cuisine. To make this possible, each steel knife is gripped by the robot arm and held against the grinding machine. Depending on the desired blade edge, the grinding robot works at a specific angle, with appropriate repetitions and the necessary pressure. A KUKA robot is also used for engraving; the KR AGILUS etches the logo into the steel.
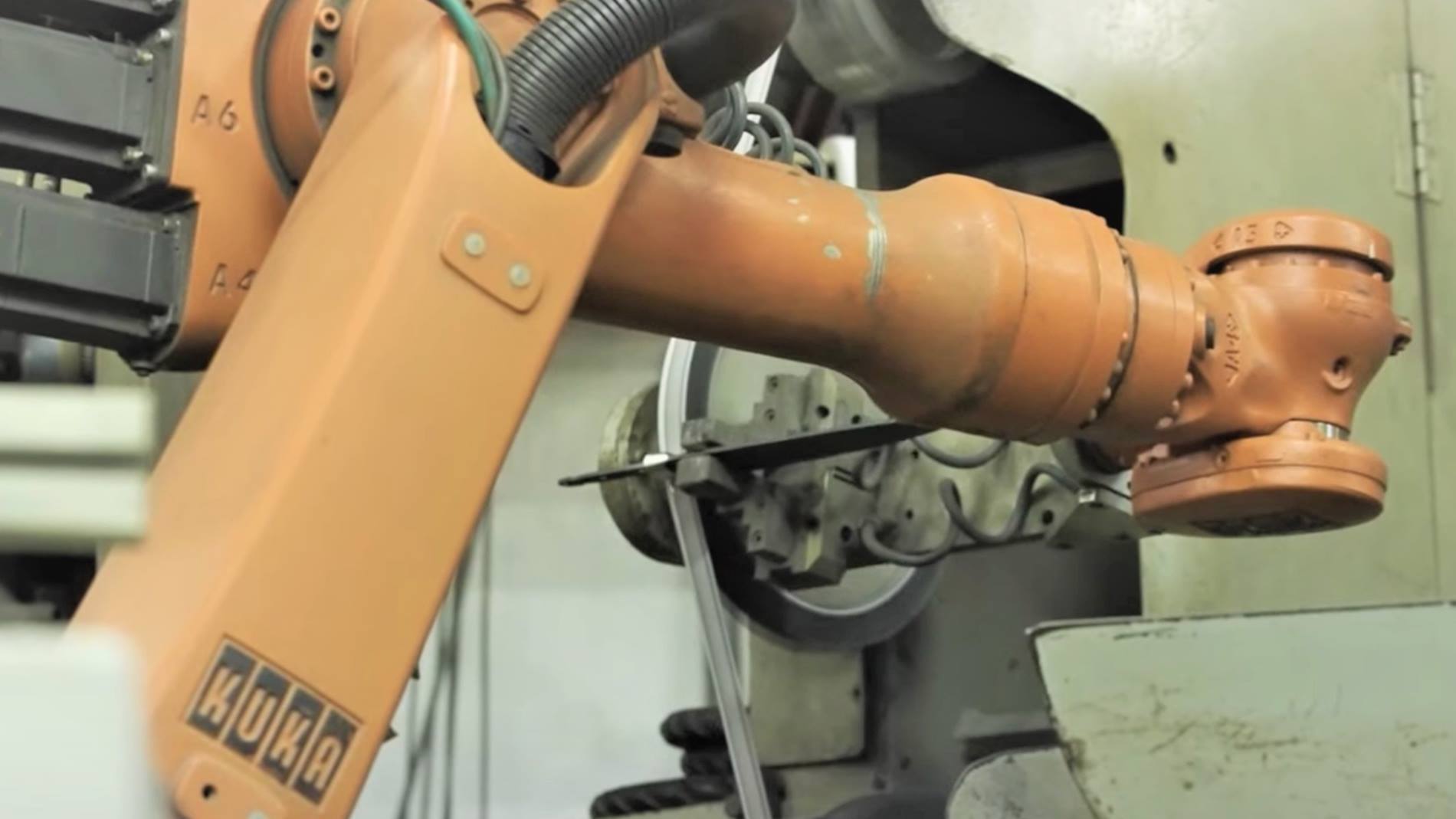
Durable robots and high product quality
What the company management really appreciates is that the KUKA robots require little space, allow maintenance in real time and enable high repeatability. And they support production for a long time: more than 20 years ago, Liow-Shye bought the first KUKA robot, which is still in operation today. The company has been able to reduce defect rates and material consumption as well as to ensure consistently high product quality. As a result, more than 30 KUKA robots now support the company's approximately 160 employees. Read more and watch the video.
3. Sustainable: Reusable plastic cutlery made by a robot
A university project started this success story: students at Reutlingen University were looking for alternatives to disposable plastic cutlery. Together with their professor, Prof. Dr. Steffen Ritter, they decided to develop sustainable reusable cutlery made of high-performance plastic. They found the right project partners in the Southern German company Gindele – a specialist in high-quality injection molded products – as well as KUKA and the KUKA system partner robomotion. Their collaboration made it possible to produce cutlery in high volumes. That’s how it works: The plastic is molded into the desired cutlery shape in an injection molding machine.
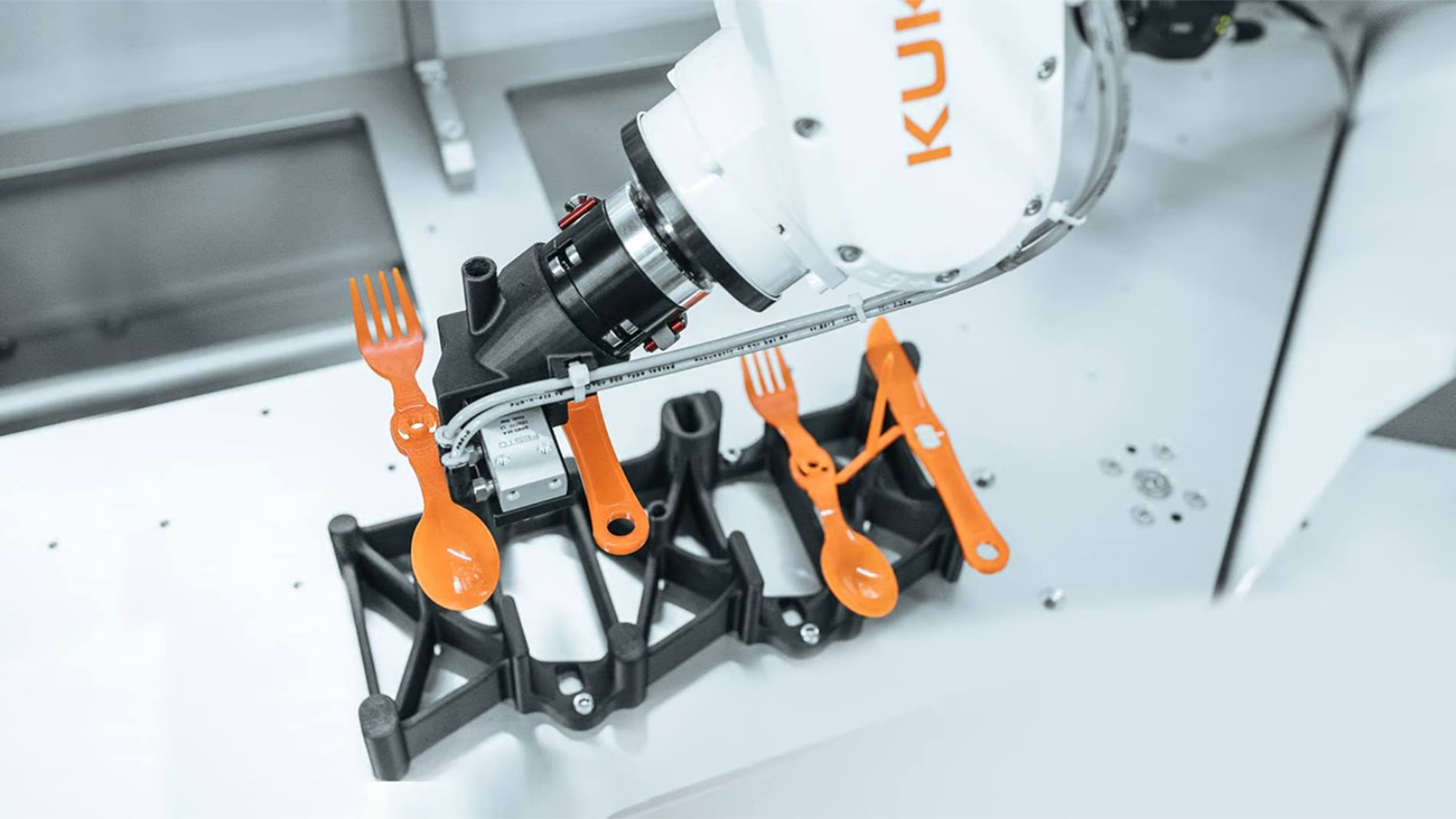
Robot with 3D-printed gripper
The highly flexible robot cell flexobot performs the handling at the injection molding machine as well as the complex further processing tasks. The heart of the cell is a six-axis KR AGILUS, which is extremely flexible and grips even complex components reliably. The robot removes the finished molded cutlery from the injection molding machine and feeds it to a vision system for quality inspection. Since the component is still very hot, it is first set down to cool down. Afterwards the robot picks the component back up and removes the sprue. The KR AGILUS is equipped with a 3D-printed gripper for this purpose.
High quality, lots of flexibility
The approximately 60 Gindele employees and the university team are extremely satisfied with the results: The flexobot has proven to be slender enough to be positioned in the immediate vicinity of the injection molding machine and flexible enough to be used for different projects. The quality of the reusable cutlery is also impressive. To read the full report and watch the video, click here.
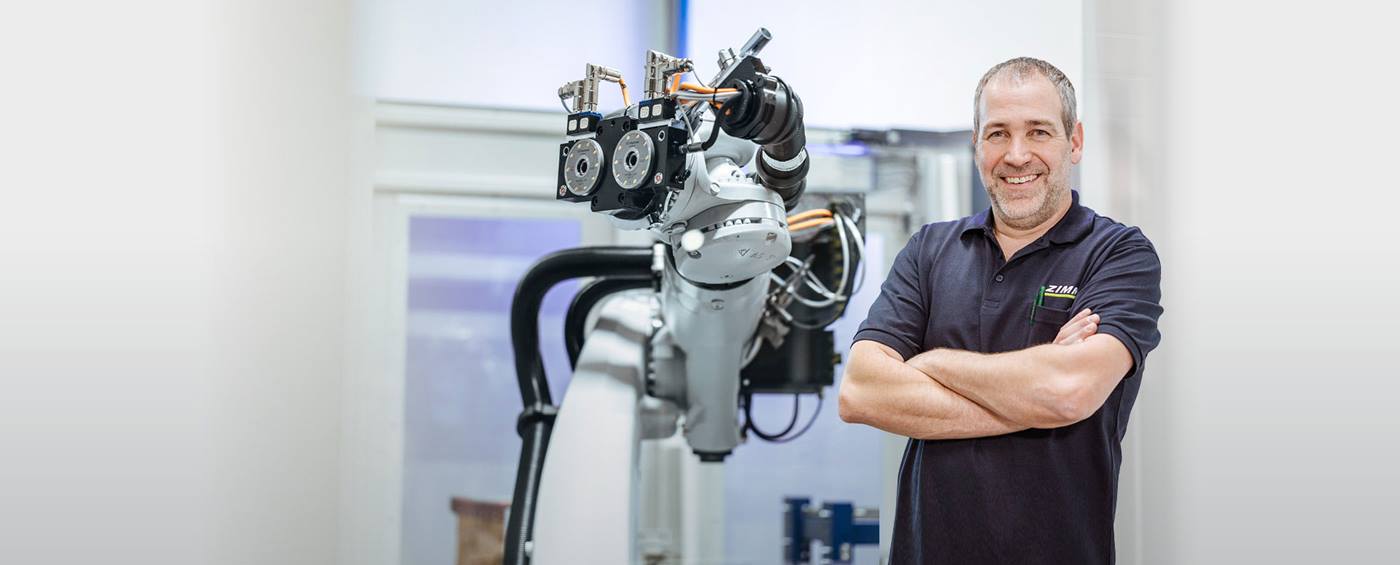
Next article