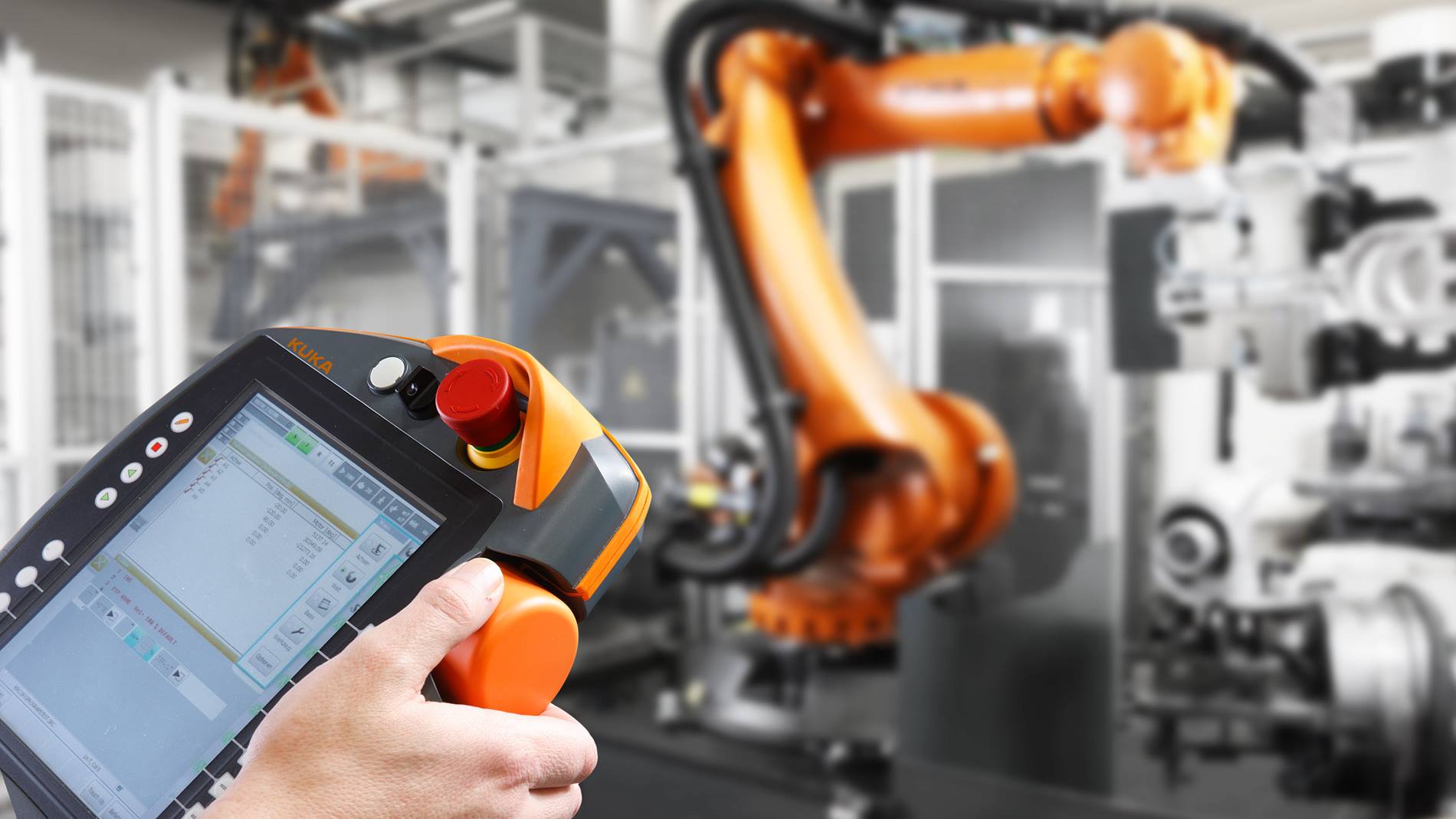
KUKA.SystemSoftware
The KUKA.SystemSoftware – KSS for short – is the operating system and thus the heart of the entire robot controller for the majority of the KUKA robot portfolio – including traditional 5- and 6-axis robots, as well as the new KR SCARA and KR DELTA robots.
Get acquainted with the basic functions of the operating system
The “functional twins” KSS 8.6 and 8.7 offer new functions without changing the existing programming environment and user interface – if you are familiar with KUKA.SystemSoftware and KRL (KUKA Robot Language), you will immediately feel at home.
And thanks to the expertise that we have built up over decades, combined with feedback from our customers, the current KSS versions 8.6 and 8.7 are the result of internal and external feedback. In combination with inline forms, project-based engineering and project-independent online programming, it is clear that KUKA has listened to the suggestions and wishes of users during the development of KSS.
Safe robot
- Extended, safe monitoring of the robot
- Assurance of system safety
- Switchable workspaces/protected spaces, safe tools
- Additional monitoring features tailored to actual needs (KUKA.SafeOperation, KUKA.SafeRangeMonitoring or KUKA.SafeSingleBrake)
Cooperating robots
- Shared workspaces
- Load sharing with up to 6 robots in a KUKA.RoboTeam
Data exchange
- TCP/IP data communication (binary/xml) to external systems with KUKA.EthernetKRL
Sensor applications
- Real-time capable sensor connection/communication through KUKA.RobotSensorInterface or KUKA.ForceTorqueControl
- Graphical programming with RSI Visual and RSI/O mapping in KUKA.WorkVisual
IT security
- Protection of the controller against malware through:
- KUKA.USB Port Security
– KUKA.Ikarus T3 antivirus solution
– KUKA.CPC – KUKA’s own whitelisting procedure
– Option to limit the use of USB ports on KUKA controllers
Conveyor
- Synchronization of robot motion with the motion of conveyor systems/components by means of the KUKA.ConveyorTech technology package

Safe communication
- Dual-channel technology interfaces XG11/XG13 or
- safe field bus communication via Ethernet-based protocols (PROFIsafe via KUKA.Profinet M/S, CIP Safety via KUKA.EthernetIP, FSoE via EtherCAT master-master gateway)
User login
Additional login methods via KUKA.Userkey
- Use of USB sticks as a key medium
- Login via external systems such as Euchner keys
- Personalized login via AD integration
Expansion of the basic functionality
- Integrated deterministic Soft PLC
- Access to I/O system and host system using KUKA.ProConOS
Technology modules
- KUKA integrators and end customers can expand the library of available KUKA inline forms and status keys according to customer requirements by using KUKA.UserTech technology.
- With the KUKA.OptionPackageEditor, these modules can be quickly and easily integrated into the KUKA system.
- Other possible modules are preconfigurations of KUKA technologies (KUKA.HMI solution, KUKA.GripperSpotTech configuration, KUKA.RobotSensorInterface context)
Customer-specific interfaces
The KUKA.HMI product family offers the possibility of creating customer-specific user interfaces at two different levels of complexity.
- For simple applications – KUKA.HMI easy
- For expert users – KUKA.HMI zenon

Vision – in 2D and 3D
- KUKA.VisionTech offers tools for 2D object recognition, quality recognition,
code and optical character recognition (OCR) - Customers can implement any of the 3D vision applications from Roboception
Design, development and expansion
Engineering functions of the KSS operating system cover everything
From the creation of your own customer-specific software packages to the visualization and simulation of your manufacturing process and on to the evaluation of complete robot cells –
- on a project basis. Configuration of the controller using database and catalog-based projects – created using KUKA.WorkVisual.
- Soft PLC interface. Integrated interface in KUKA.WorkVisual to KUKA.Multiprog – the Soft PLC engineering environment of KUKA.ProConOS.
- Load data determination. Determination of the load parameters of real tool attachments by means of pendulum motions using the KUKA.LoadDataDetermination option.
- Simulation. Design and evaluation of complete robot cells using KUKA.Sim.
- Virtual robot controller. Virtualized version of KUKA.SystemSoftware (KSS) available as KUKA.OfficeLite.
- Customer-specific technology packages. Creation of your own customer-specific software packages using KUKA.OptionPackageEditor. Further modules are provided here by the expansion technologies KUKA.UserTech and KUKA.HMI easy.
- Recovery. Image-based backup solution using KUKA.Recovery.