
KUKA automates laser system for automotive supplier Proseat
Proseat uses the automation solution from KUKA for the production of seat elements for BMW. The laser system from the Augsburg-based company enables the clean cutting of workpieces, despite complex 3D geometries. It is thus a higher-quality solution than the die-cutting process that was initially planned.
The task
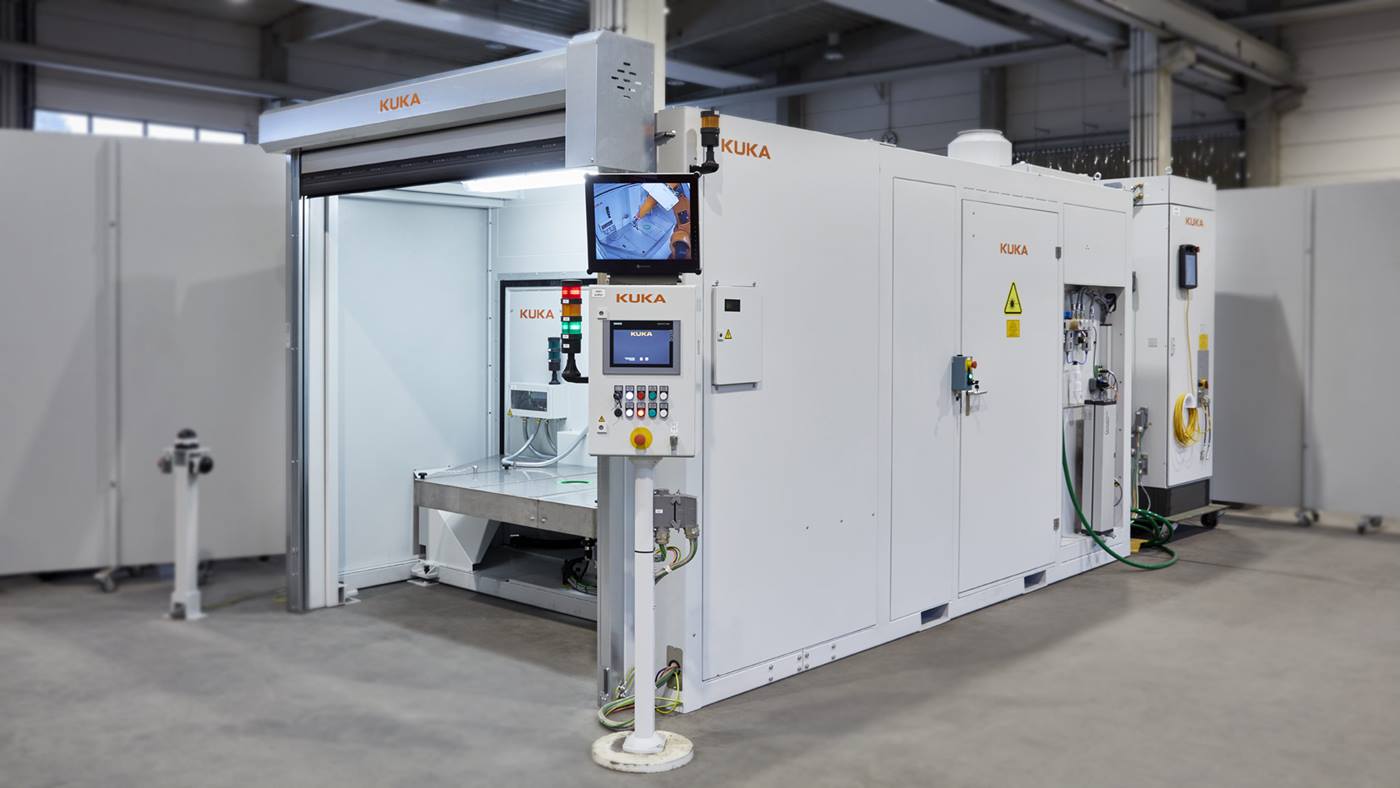
The solution
Two automated laser systems from automation specialist KUKA are used at the plant in Poland. Unlike mechanical cutting, the process is:
-
precise,
-
wear-free and
-
clean
Because of these advantages, laser cutting has successfully asserted itself in metalworking. With non-metallic components, on the other hand, this technology has not yet become established. That is no reason for KUKA not to use lasers. KUKA has already devoted itself intensively to this topic and experimented with various different materials.
At the Obernburg site, employees have spent almost 20 years tinkering with solutions that enable various materials to be processed as efficiently as possible. The company implemented its first laser automation cells for VW as far back as 1998. Today, more than 300 systems are in use at various customers’ plants. Proseat benefited from the experience and process expertise of the Augsburg-based company: the covers for the left-hand and right-hand side bolsters are produced by means of laser sublimation cutting in a 50-second cycle. At the heart of the system is a CO2 laser robot. With its integrated beam guidance, the robot is more flexible and dynamic and can reach even difficult cutting points. The system fixture too was precisely tailored to the process, being equipped with a turntable and suction cups. The KR C4 ROBOTstar robot controller rounds off the automation package: it enables simple control and provides a clear overview of the system. Compared to the die-cutting process that was originally planned, laser cutting offers many advantages:
- Reduced programming effort: modifications to the vehicle body can be taken into consideration right up to the last moment.
- No wear to the tools, as no forces are applied to the component.
- Energy and cost savings: the energy input of the KUKA CO2 laser robot can be adapted exactly to the specific machining process.
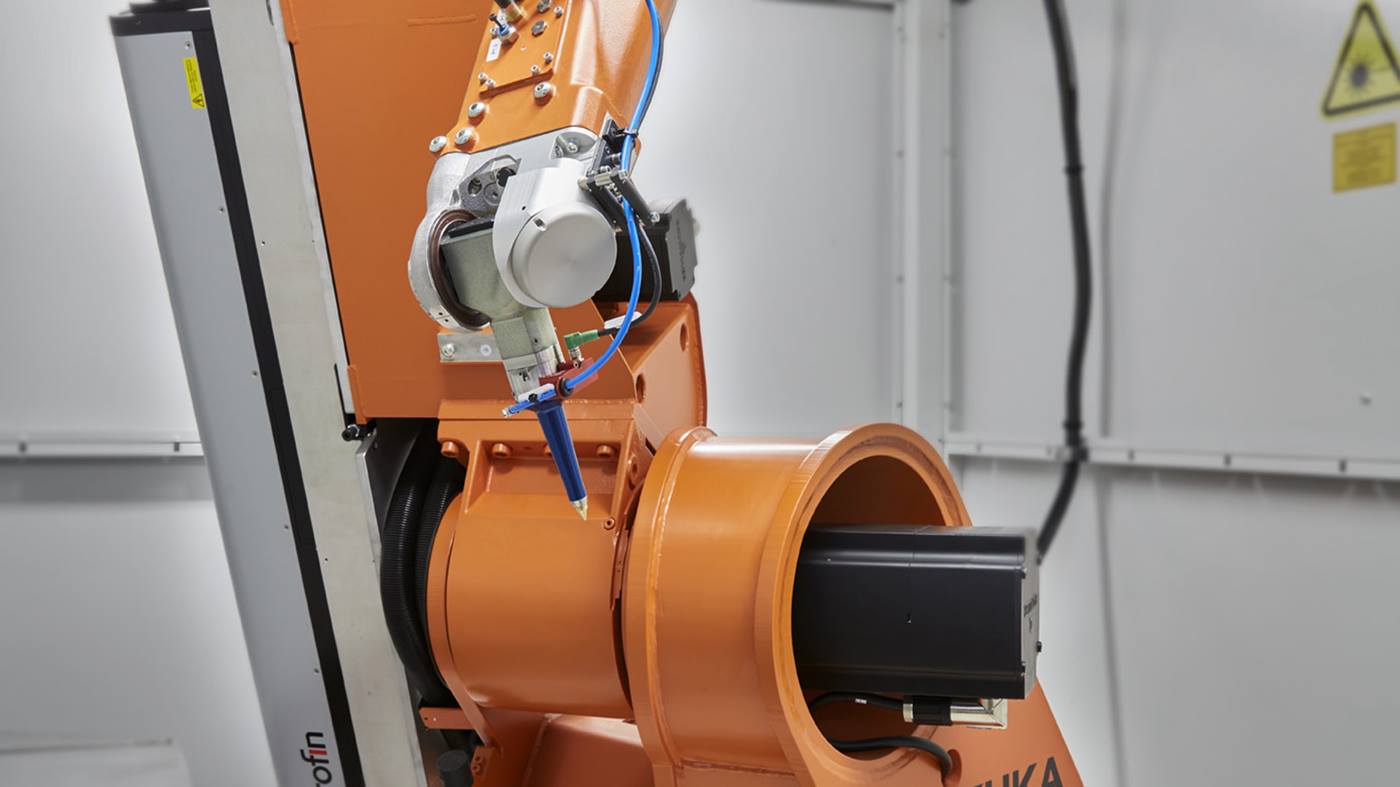
Particular expertise is needed here, as the characteristics of the materials vary greatly.
