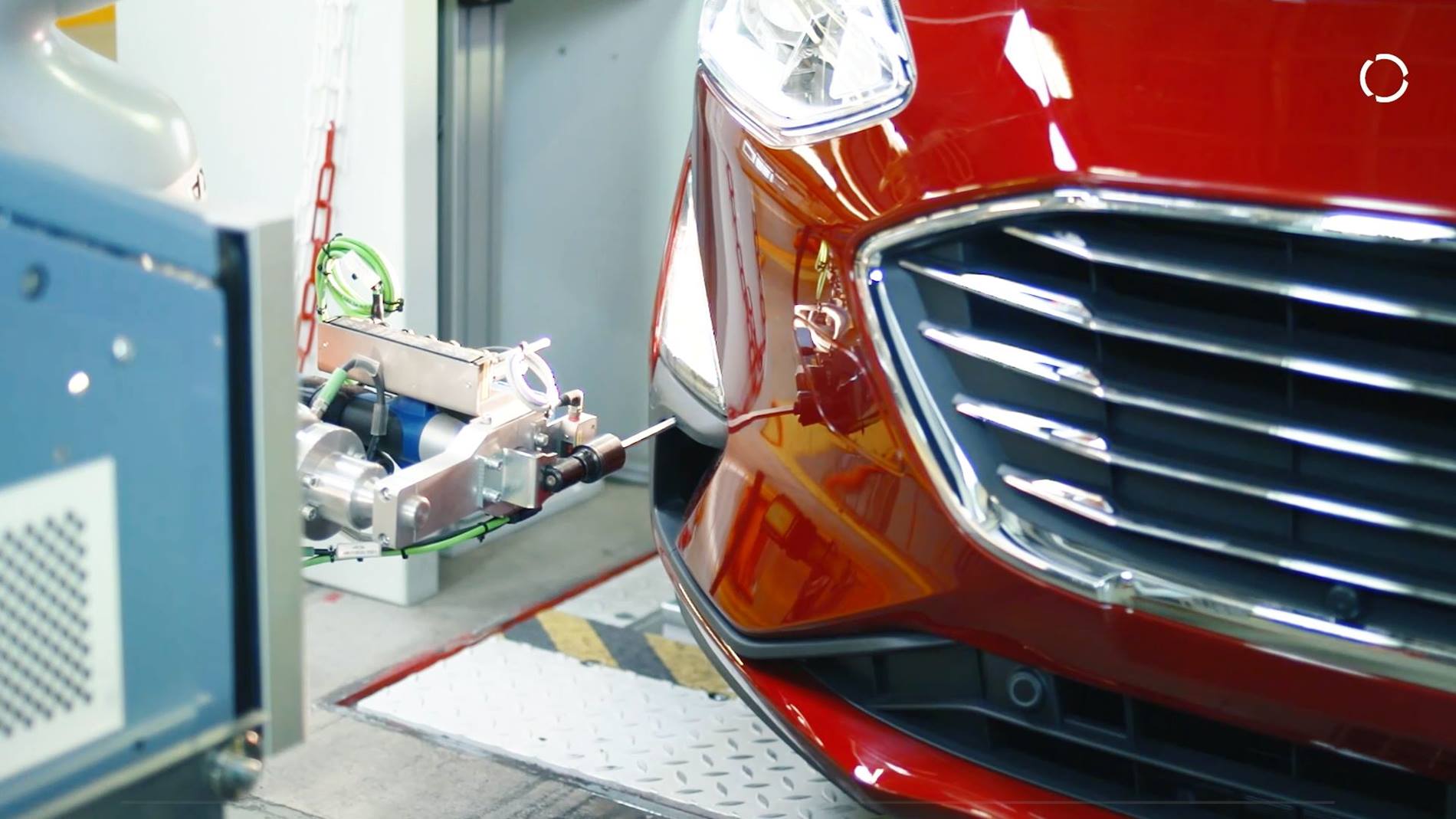
Human-robot collaboration during headlight adjustment
To reduce the strain on the workers, two LBR iiwa cobots perform the unergonomic task of adjusting fog lights at Ford. Parallel to this, human colleagues can adjust the main headlights.
In the automotive industry, vehicle fog lights have previously been adjusted manually by human operators. While stooped over, the human operator searches for the hard-to-reach opening for the adjusting screws in the bumper area. Once he has found the adjusting screw, he positions the tool on it extremely carefully without damaging the adjustment opening on the bumper.
The solution
To provide relief for the human worker during this ergonomically unfavorable work and simultaneously achieve an improved adjustment quality, Ford VOME (Vehicle Operation Manufacturing Engineering), Dürr Assembly Products and KUKA have jointly developed an innovative alternative concept for the conventional process as part of a feasibility study. The solution called for the use of the KUKA LBR iiwa cobot. The sensitive robot adjusts the fog lights fully automatically. In doing so, humans and robots work on the same vehicle without additional safety equipment.
The secret of the HRC concept
Among other things, the intelligent industrial work assistant KUKA LBR iiwa stands out for its ideal size and joint torque sensors. With these, the LBR iiwa detects contact immediately and reduces its level of force and speed instantly. These characteristics make it possible to work with human operators in confined spaces. Furthermore, with its high-performance servo control, the cobot detects contours quickly under force control. In combination with an end effector specially developed by Dürr (consisting of a camera system and an adjustment screwdriver), the KUKA LBR iiwa positions the adjustment screwdriver according to the hole coordinates acquired by the camera system. The adjusting screw itself is located approximately 80 mm behind the hole in the bumper. Thanks to sensitive movements, the KUKA LBR iiwa cobot optimally positions the adjustment tool into the screw head.
Redundant safety is provided by the HRC-capable, heavy-duty aluminum gantry from Dürr Assembly Products – on which the KUKA LBR iiwa is positioned in a ride-on installation above the light collecting box directly in front of the headlight to be adjusted. The advantage here: additional robot positioning can be dispensed with.
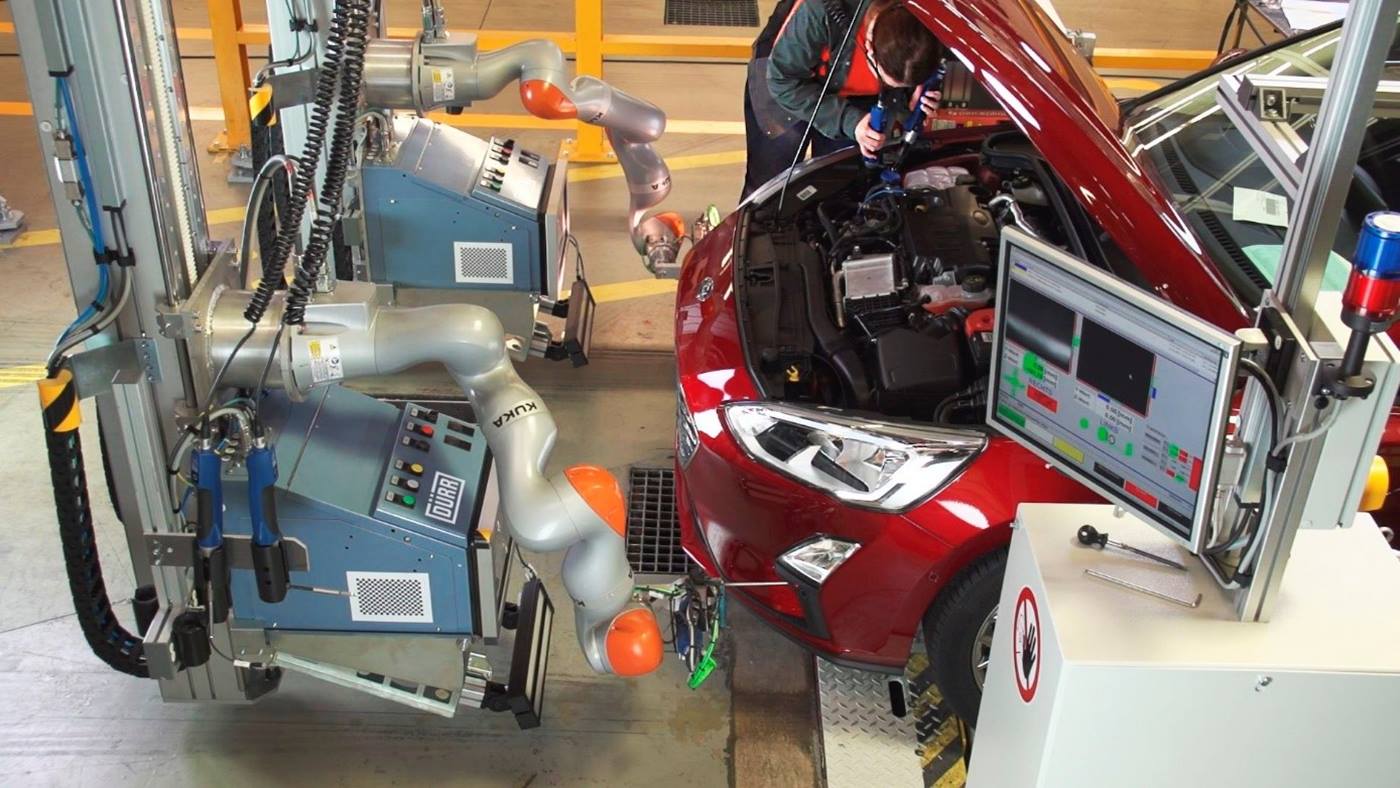
Award-winning quality
The advantages of the innovative automation concept are convincing:
- Relief for the human worker during ergonomically unfavorable tasks
- Improved quality of the adjustment of the fog lights
- Time savings for the entire adjustment process thanks to the adjustment of the fog lights by the KUKA LBR iiwa cobot on the one side of the body and simultaneous adjustment of the main headlights by a human worker on the other side of the body. Following this, adjustment is carried out alternately for the other side.
As a result of this, KUKA Automatisering + Robots N.V. in Belgium and Dürr Assembly Products have been given the “Aligned Business Framework World Excellence Award” at the 20th Ford World Excellence Awards for their outstanding performance as global suppliers.
