
KUKA Showcases Automation for Human/Machine Collaboration at ATX West
During the ATX West show, KUKA Robotics showcased several new technologies geared specifically for safely automating those manufacturing processes where humans interact with robots on a regular basis. Among those technologies were the new LBR iisy cobot, the new KUKA KMP 600-S diffDrive automated mobile platform and the company’s LBR iiwa robot incorporated into an automated mobile robotic material-handling system.
January 25, 2023
Referred to as Sensitive Cobotic technology, KUKA’s LBR iisy represents the future of automation. The cobot is ready-to-use automation that quickly and easily integrates into any manufacturing application from pre-defined production processes to open, unstructured work environments with unpredictable conditions from one job to the next.
Whether loading/unloading machines, assembling components or packaging, the cobot provides increased versatility and can be immediately operated by anyone from an automation expert to a cobotics newcomer. Featuring various operator levels, the user-friendly system adapts to the corresponding level of user knowledge.
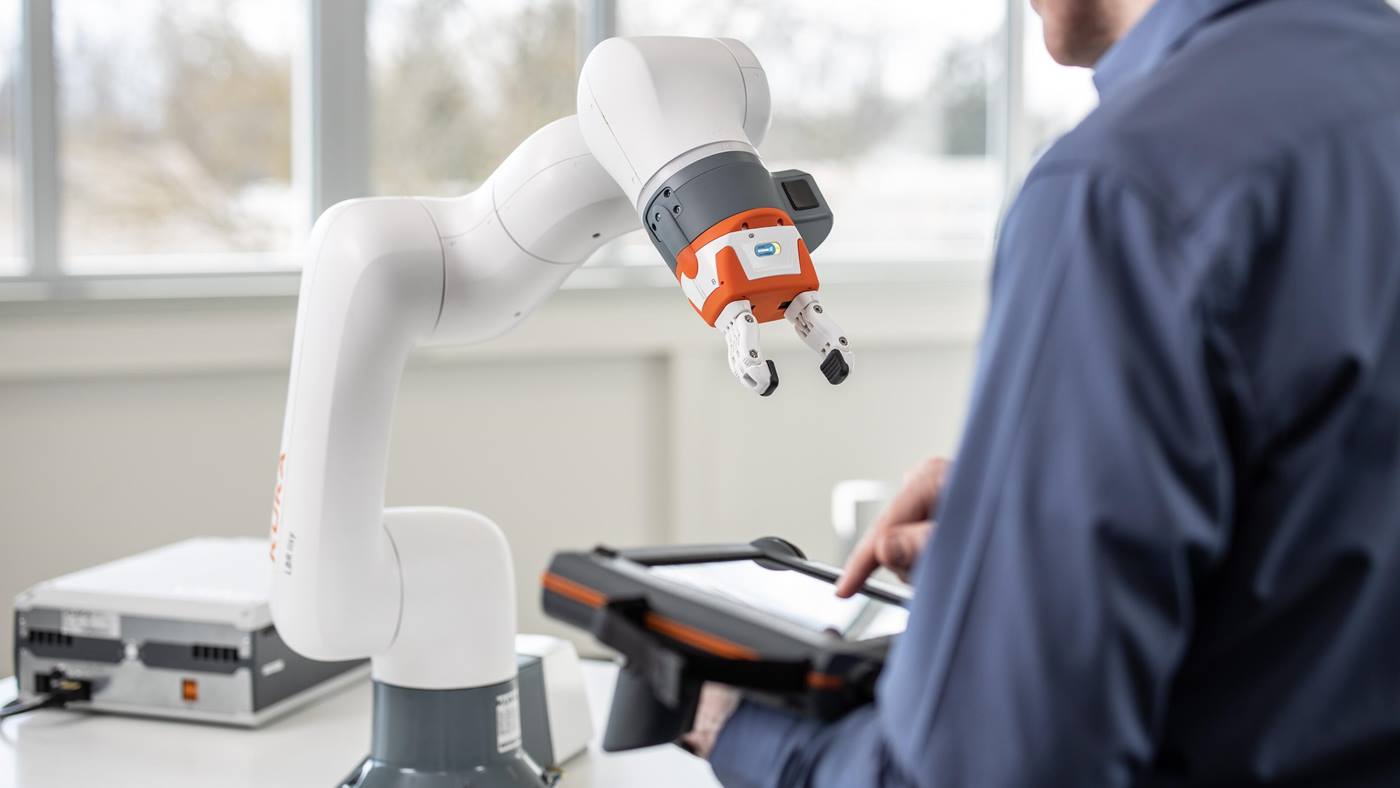
