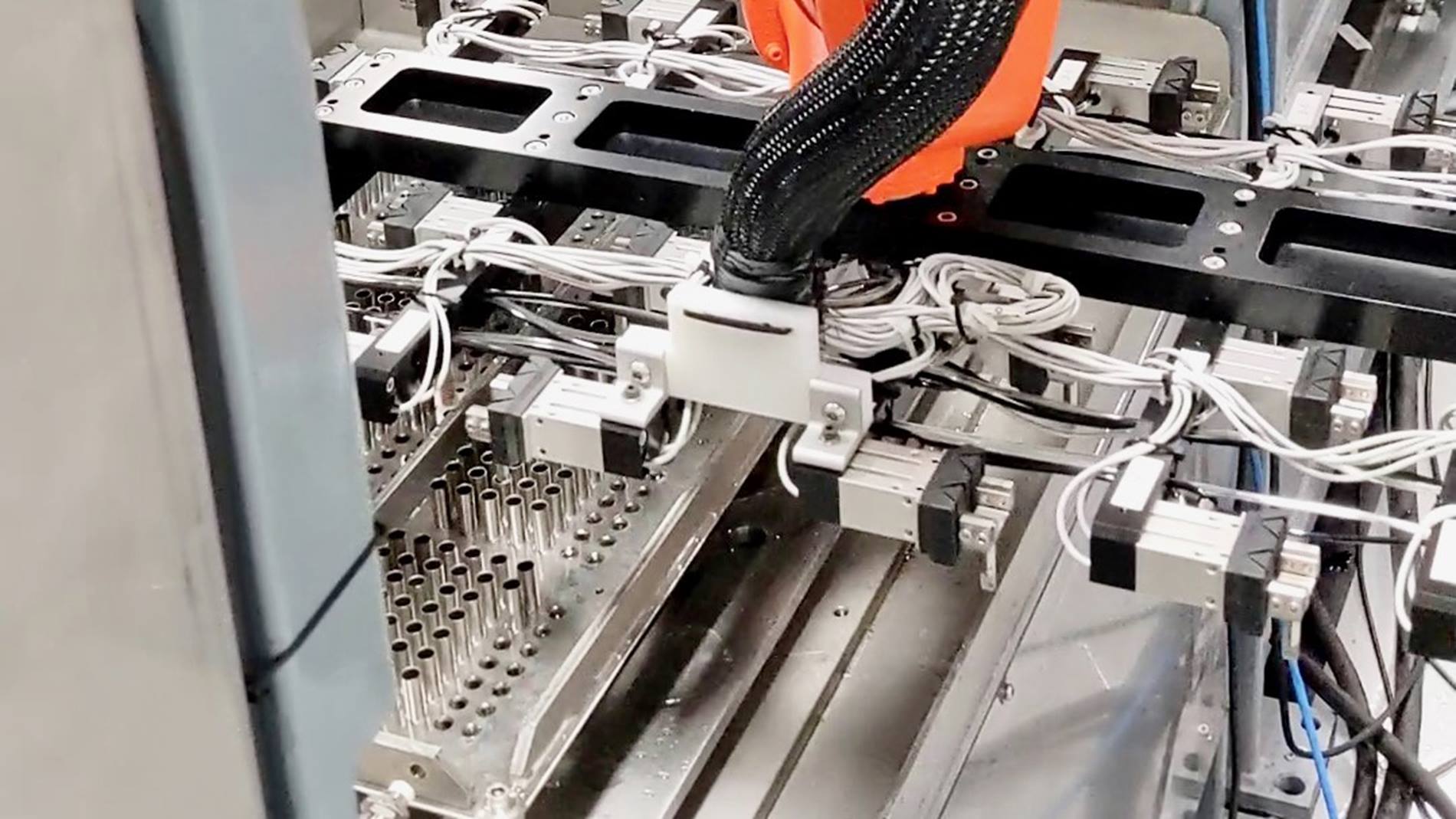
Voxel Innovations Relies on KUKA Automation for PECM Part-Production Line
Voxel counts on KUKA Robotics to automate its pulsed electrochemical machining production.
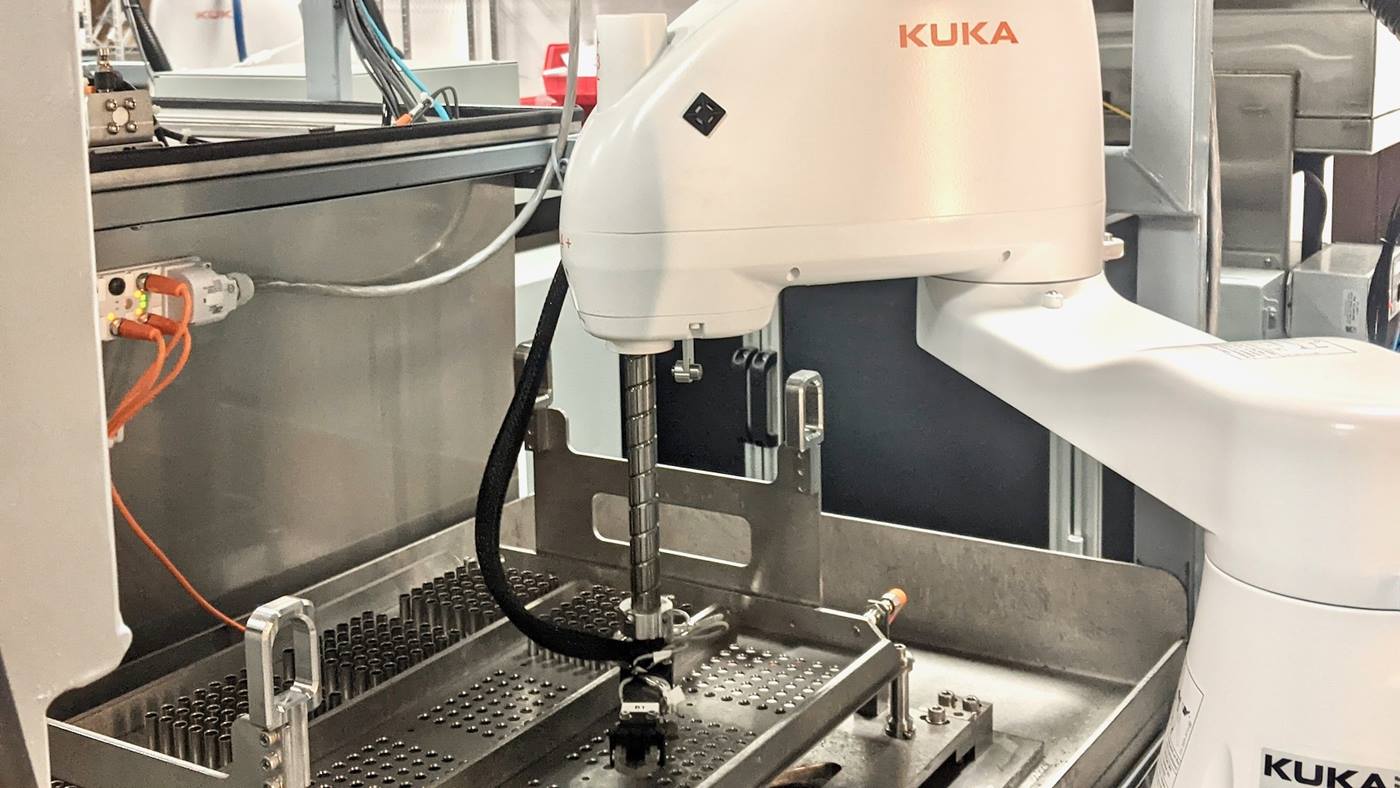
Unlike conventional machining, PECM is a non-contact, non-thermal material removal process that passes electrical current between a tool (cathode) that is the inverse of the workpiece geometry and the workpiece (anode).
The technology is extremely precise with virtually no tool wear and can produce thousands of parts with less than 10 µm repeatability. Additionally, PECM machines and finishes parts in a single step with surface quality that eliminates the need for secondary surface finishing operations. PECM is particularly well-suited for high-volume processing of metal alloys often impossible to cut with conventional machining operations.
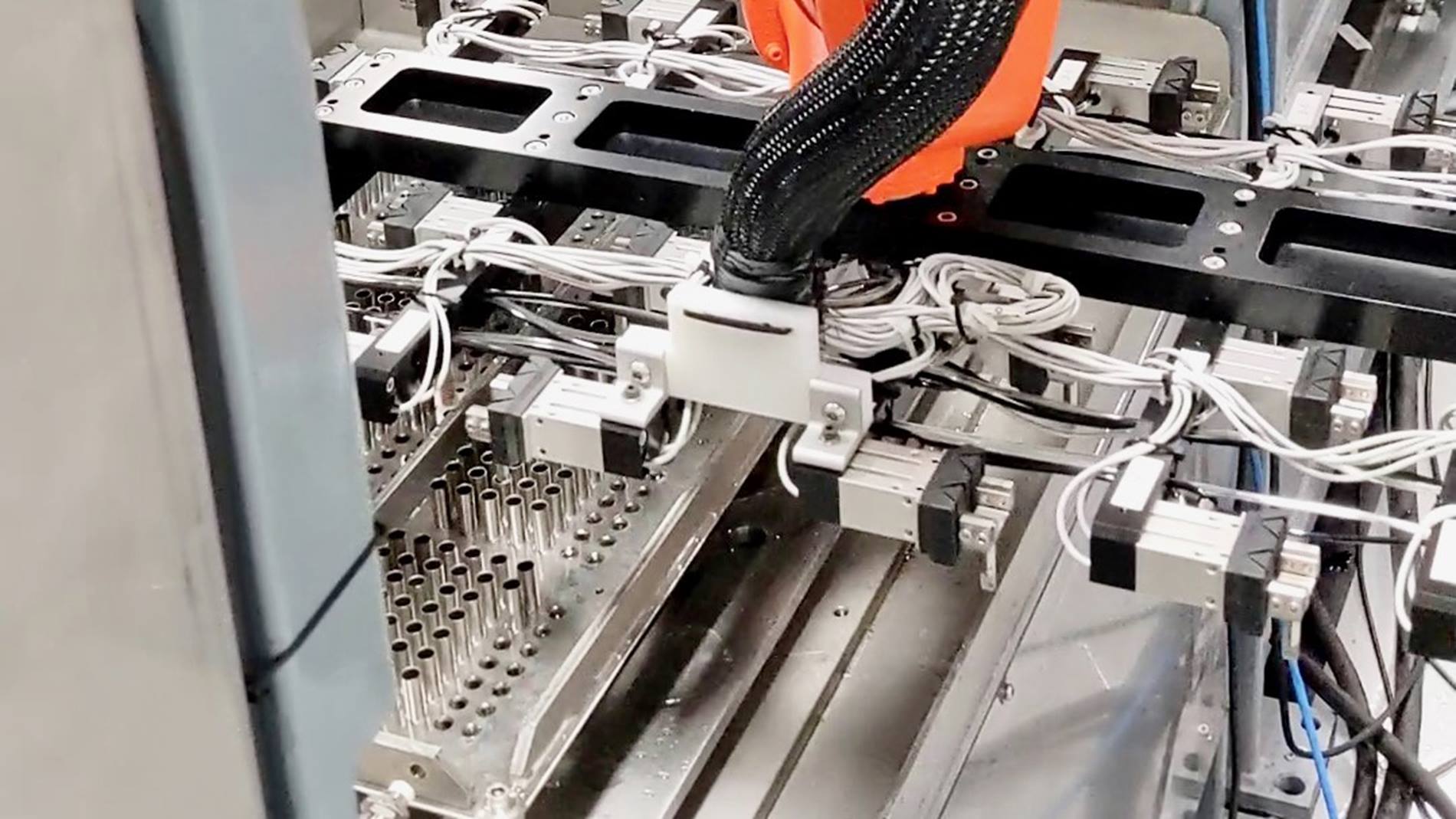
Voxel can create complex 3D geometries in delicate parts with no deformation and produce multiple features and parts in parallel for incredibly high-volume throughputs. In fact, the company does so at levels that are exponentially greater than die-sink or wire EDM methods.
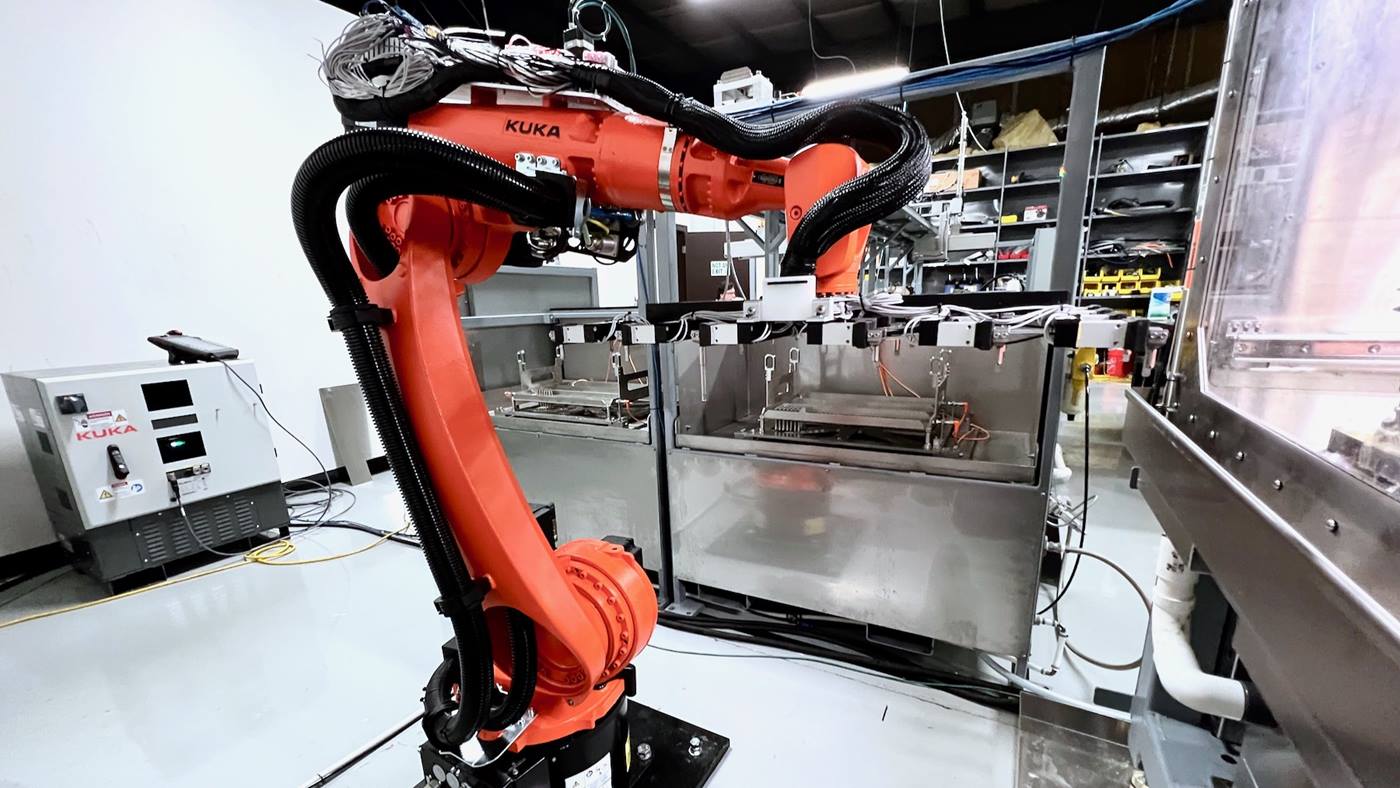
On the front end, the SCARA’s precise, high-speed parts-handling capability expedites individual part loading, while the second SCARA takes separate parts through multiple inspection processes once the part is completed. The six-axis CYBERTECH equipped with a 24-gripper end effector capitalizes on its long reach and precision to quickly load and unload parts from a cleaning tank to the PECM machine and back into a second cleaning tank.
In addition to providing greater throughput, the KUKA automation frees operators to refine processes and problem-solve.
It also drives cost per part down, reduces scrap risk and provides part traceability, all of which are important to Voxel’s medical, aerospace, energy and industrial customers.
Availability and overall engineering support initially drove the decision to select KUKA; however, the robots’ precision and intuitive adaptability made it clear that KUKA would be critical to Voxel’s operations. Positioning accuracy and the ability to make very fine adjustments, along with KUKA’s collision detection feature were essential to avoiding expensive miscalculations during development of the production line.
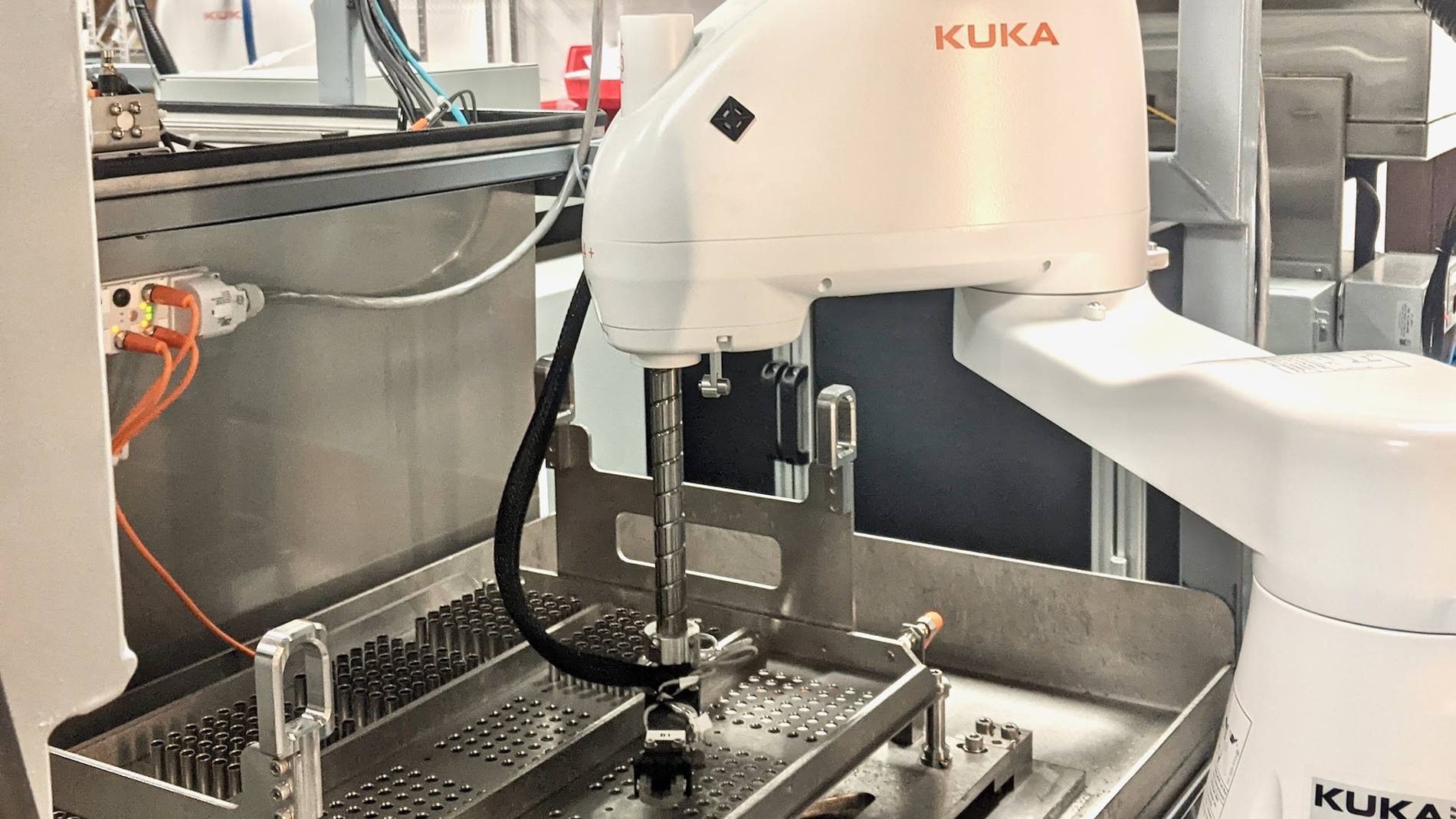
“One of the strengths we noticed working with KUKA was the application engineering support during the purchase process,” Herrington said. “We were new to the robotics field, trying to understand moments of inertia, loads and models of things we mocked up to see if they fit on different robots. We also realized we needed a slightly different robot a couple months after placing the original order, and KUKA worked with us to find a different robot to make our system come together the way we needed it.”
Integrating KUKA’s advanced robotics and automation has not only optimized and scaled Voxel’s production, it has set the tone for the company’s future.
“We have this very high-volume, sophisticated production line running now, and we will continue to stick with our simple plan of vertical integration in terms of the specialty manufacturing processes we offer customers. This sophistication will, in turn, attract new customers, and as that happens, we’ll look to KUKA for when the need comes to automate more of our production operations,” Herrington said.