
KUKA Systems solutions sort and size-reduce waste at a nuclear decommissioning facility
Automated robotic systems can build cars – or decommission nuclear sites. In hazardous environments, KUKA robots could be deployed to ensure human workers’ safety along the complete nuclear fuel cycle, from mining and enrichment to conversion. At a nuclear decommissioning facility in the UK, they currently support its decommissioning by sorting and size-reducing waste as well as swabbing and housekeeping. A second system to be installed subsequently will replace the lids on waste boxes and bolt them.
The task
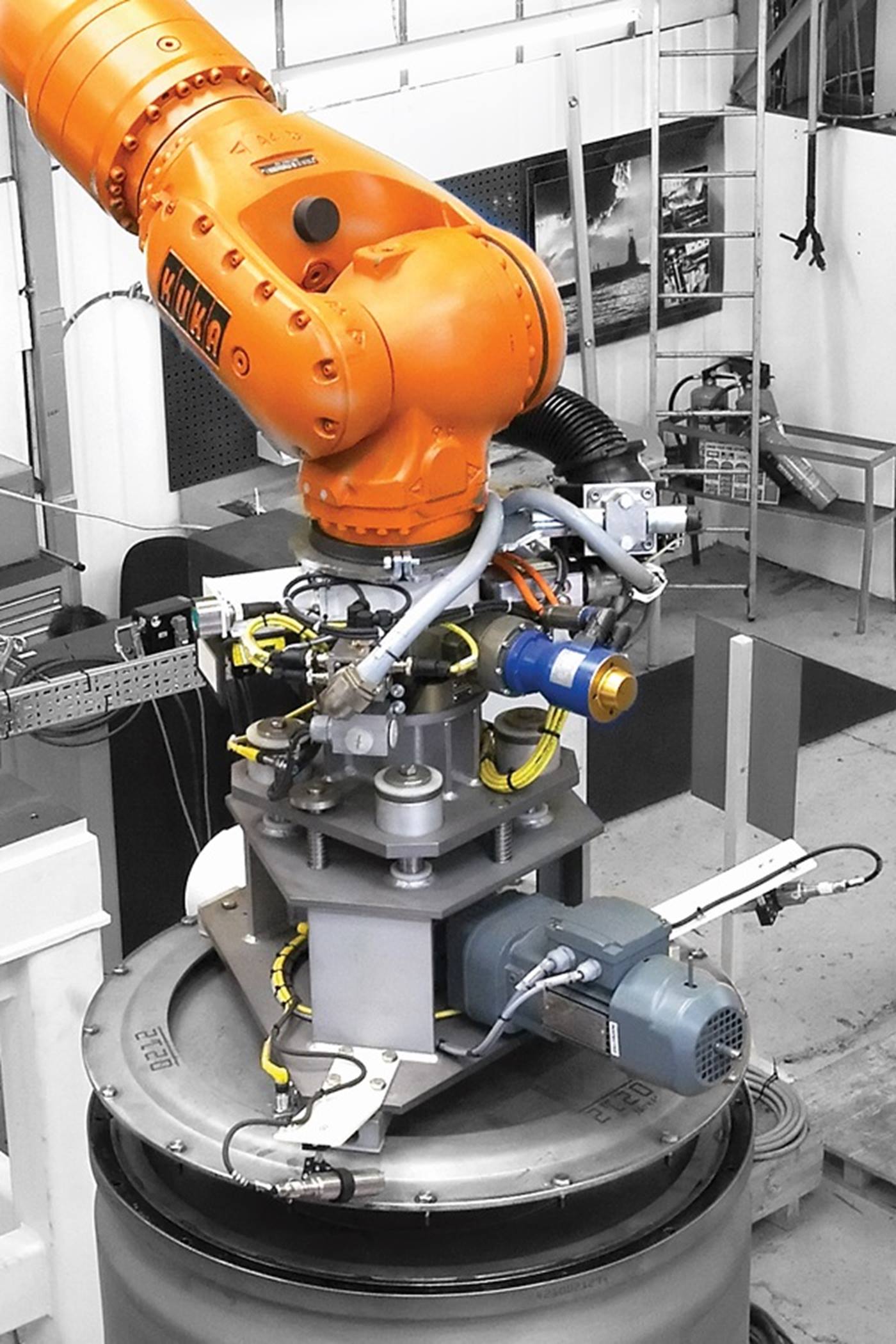
The solution

KUKA solutions with their well proven, high reliability are perfectly suited to facilitate a safer, quicker and cheaper decommissioning. Combined with outstanding technical support at the premises offered by a KUKA staff member, the automated robotic system offers the high quality results necessary for our nuclear applications.
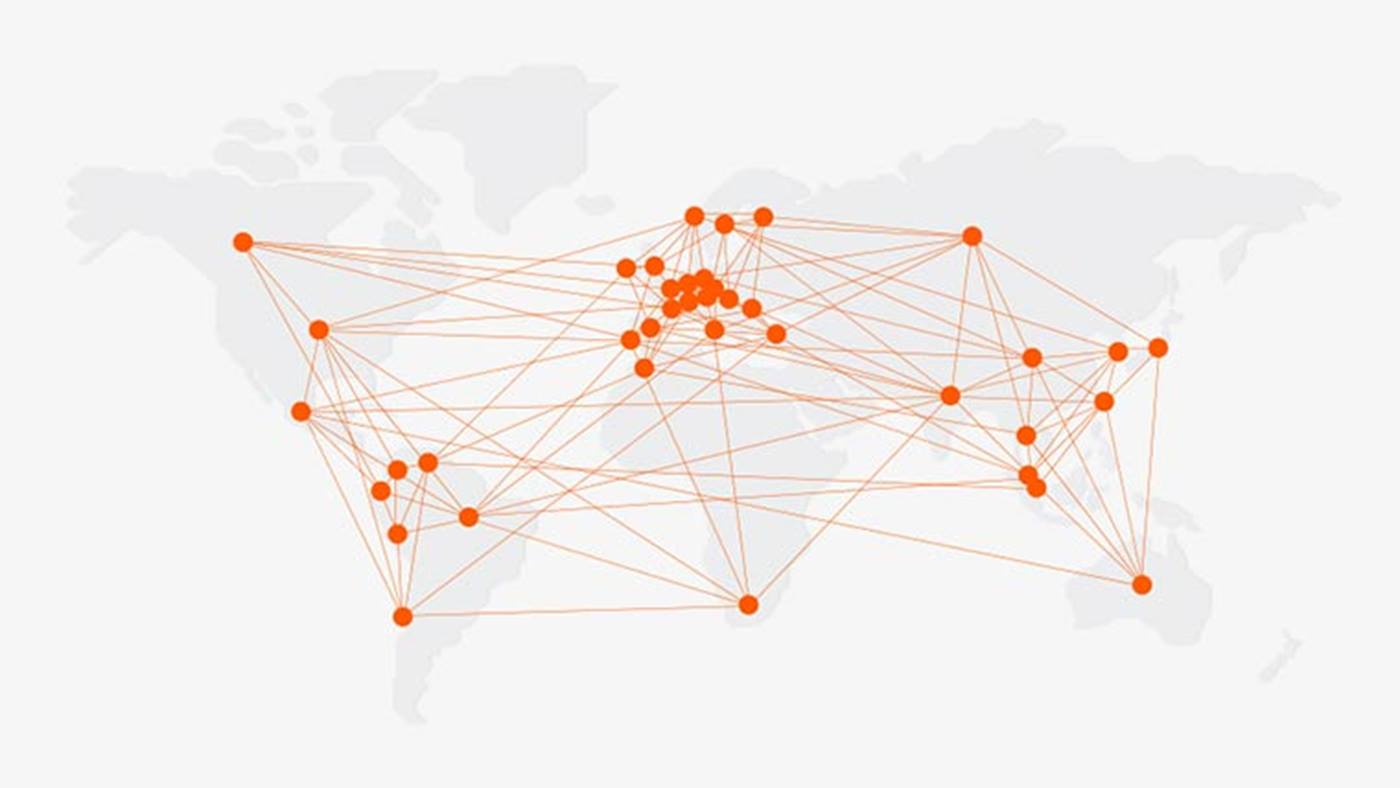