
KUKA robotic deburring machine transform foundries at Grind Master
Grind Master, a technology leader for metal processing machines, helps other companies to automate their deburring process of die-cast aluminium components. Considering the high quality requirements for visible Class A parts, two KUKA small robots of the KR AGILUS series have helped increasing the productivity and quality while at the same time lowering the overall costs.
The success story of Grind Master Machines Pvt. Ltd. began with a married couple’s passion for engineering, a small garage and an even smaller budget in 1984 in the historic city of Aurangabad. A bit over three decades later, the company has become a global technology leader and exporter for metal processing machines. In January 2016 Grind Master decided to include KUKA robots into their portfolio.
Automation solution with deburring machine for the harsh foundry environment
In deburring shops in India, usually casual manual labor is used in the production of die-cast aluminium components, such as for automobiles, scooters and motorcycles. Many of those parts are visible Class A components however, which require a high degree of consistency and quality in the finishing process. Additionally, the high temperatures, fumes and dust in the foundry prove to be straining for the human workers as well as the machines. Both to improve the work place situation as well as the productivity and quality of the deburring shop, automation suggests itself.
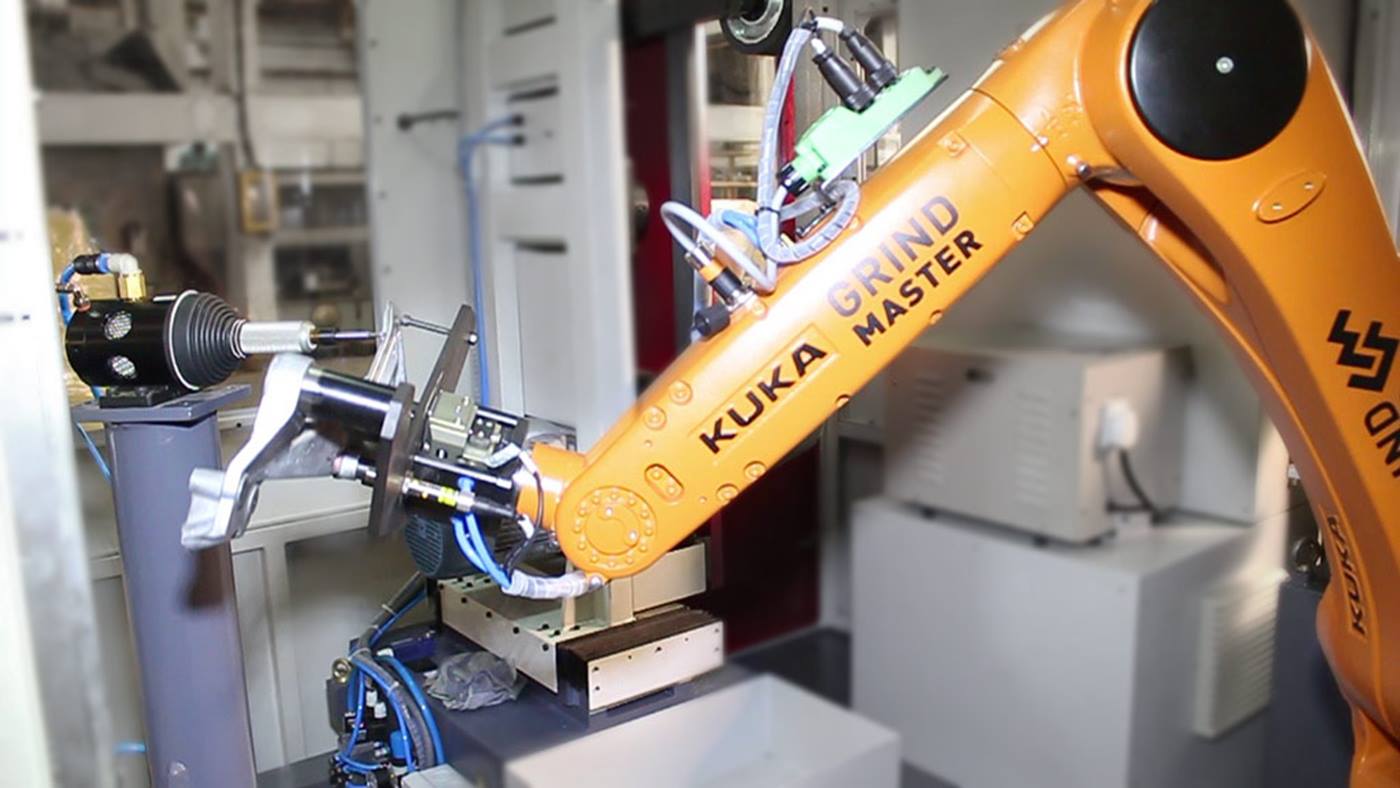
Metal deburring machine provides unmatched quality and consistency
A linear portal was out of the question for Grind Master, because the high number of component variants and frequent model upgradation made a flexible solution necessary that can be reprogrammed easily and quickly. Additionally, the complex shapes of the parts called for the mobility and speed of a six-axis robots. For Grind Master, the answer was the KUKA KR AGILUS. This small robot is not only extremely agile, fast and precise, but also very robust and compact, making it an ideal solution for the foundry environment at Grind Master. The result is a robot that deburrs the die-cast parts with unmatched consistency.
Low cycle and change over times increase productivity at metal processing
With a cycle time of 25 seconds per part and a setup change time of ten minutes, the solution has proved to more than satisfy the demanded criteria of customers such as Aurangabad Electricals Ltd. Not only has their productivity increased, but also the quality of the produced components. Through the highly advantageous cost-benefit ratio, Grind Master estimates a Return of Investment within about three years. “Robotic deburring is a transformation of the foundry and human lives therein, by creating a hazard-free, safe and healthy work environment, delivering high quality parts and matching global manufacturing practices. With the success of the first two deburring robots, we would like to proceed with automation of the entire foundry with robots for this operation,” says Sameer Kelkar, CEO of Grind Master Machines Pvt. Ltd.
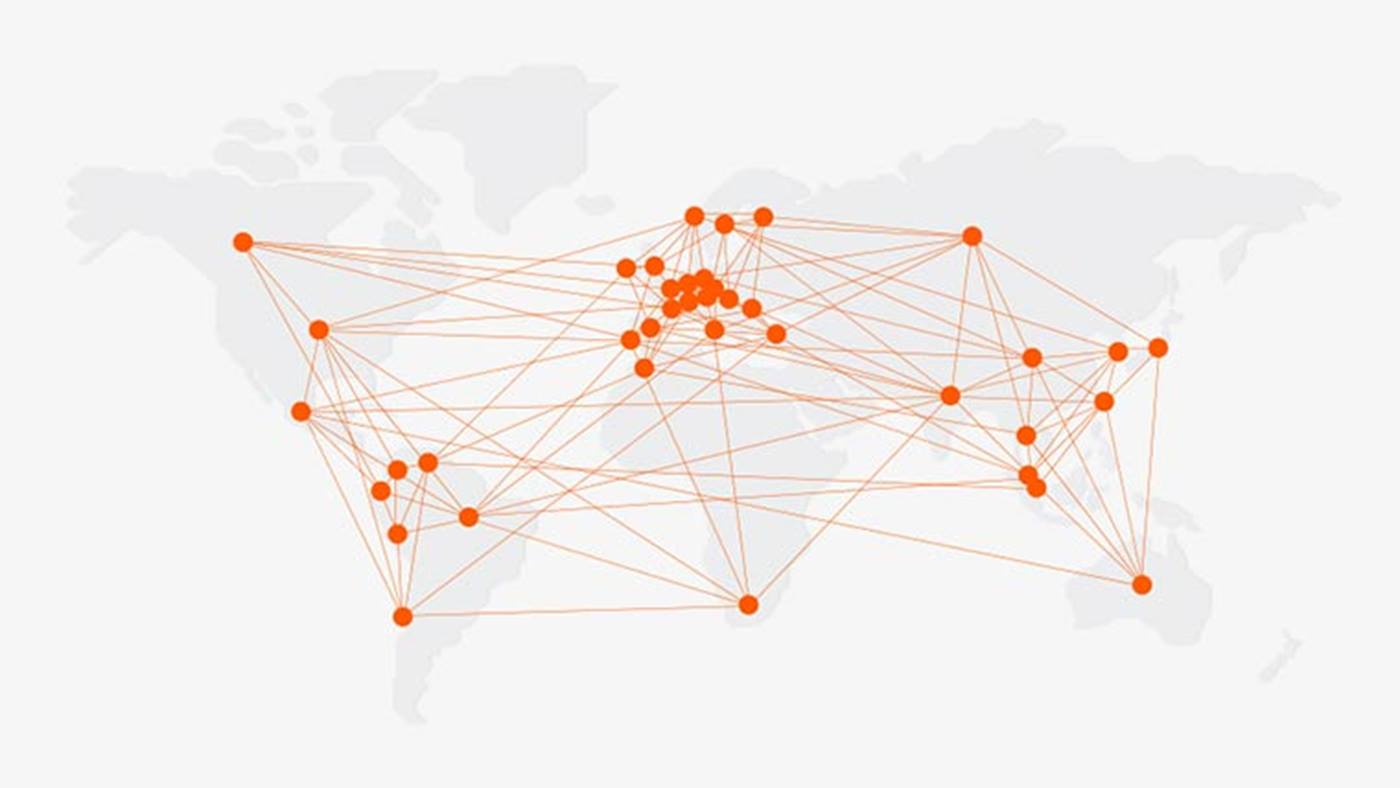