
It’s all in the mix: KUKA palletizer for beverages
In the Pepsi – Jordan ICE warehouse, a KUKA KR 700 PA stands at the center of palletizing operations. It stacks soft drinks of different shapes and sizes on the same pallet. Its long reach combined with optimal cycle times, enormously boosts productivity in the beverage manufacturer’s warehouse.
KR 700 PA: the heart of the beverage palletizing system

Mixed palletizing of beverages – challenge mastered


Precise, fast, powerful

From a manual system to beverage palletizing
Until 2016, numerous employees in the Pepsi Jordan warehouse manually performed the task that the robot now automates. The customer wanted automation to relieve the burden on the people who had to carry out this heavy physical work. “Automation was the only way to make the process as effective as possible. And KUKA had the most suitable robot for us,” said Bechara Nassar, explaining the choice of the KR 700 PA.
Pepsi also wanted the automation system to use as little space as possible. With its reach of up to 3.3 m, combined with its compact design, the KR 700 PA was thus well suited to the warehouse of the beverage manufacturer.
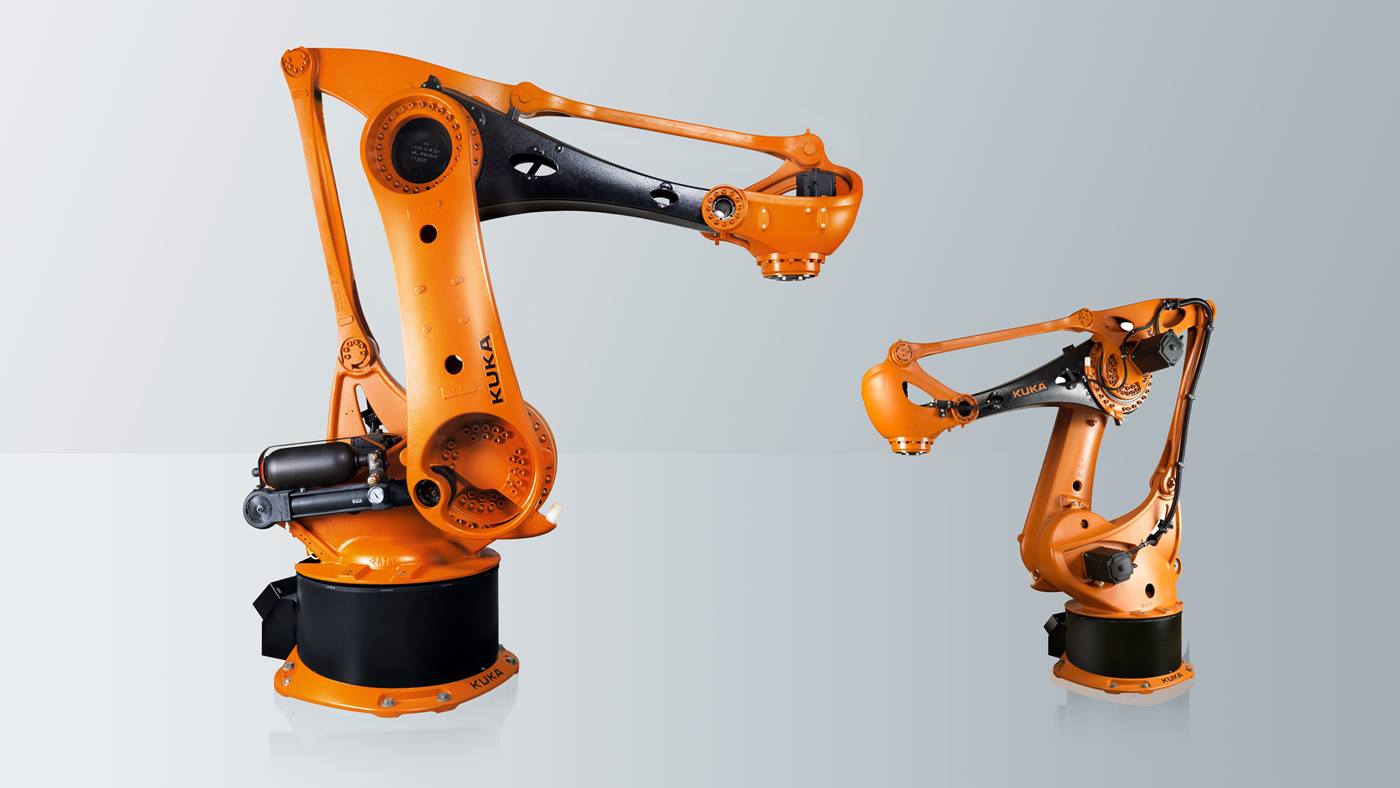
First collaboration with KUKA

We wanted to make the palletizing system for beverages as efficient as possible – in very limited space. For us, the KR 700 PA is most ideally suited for this.
