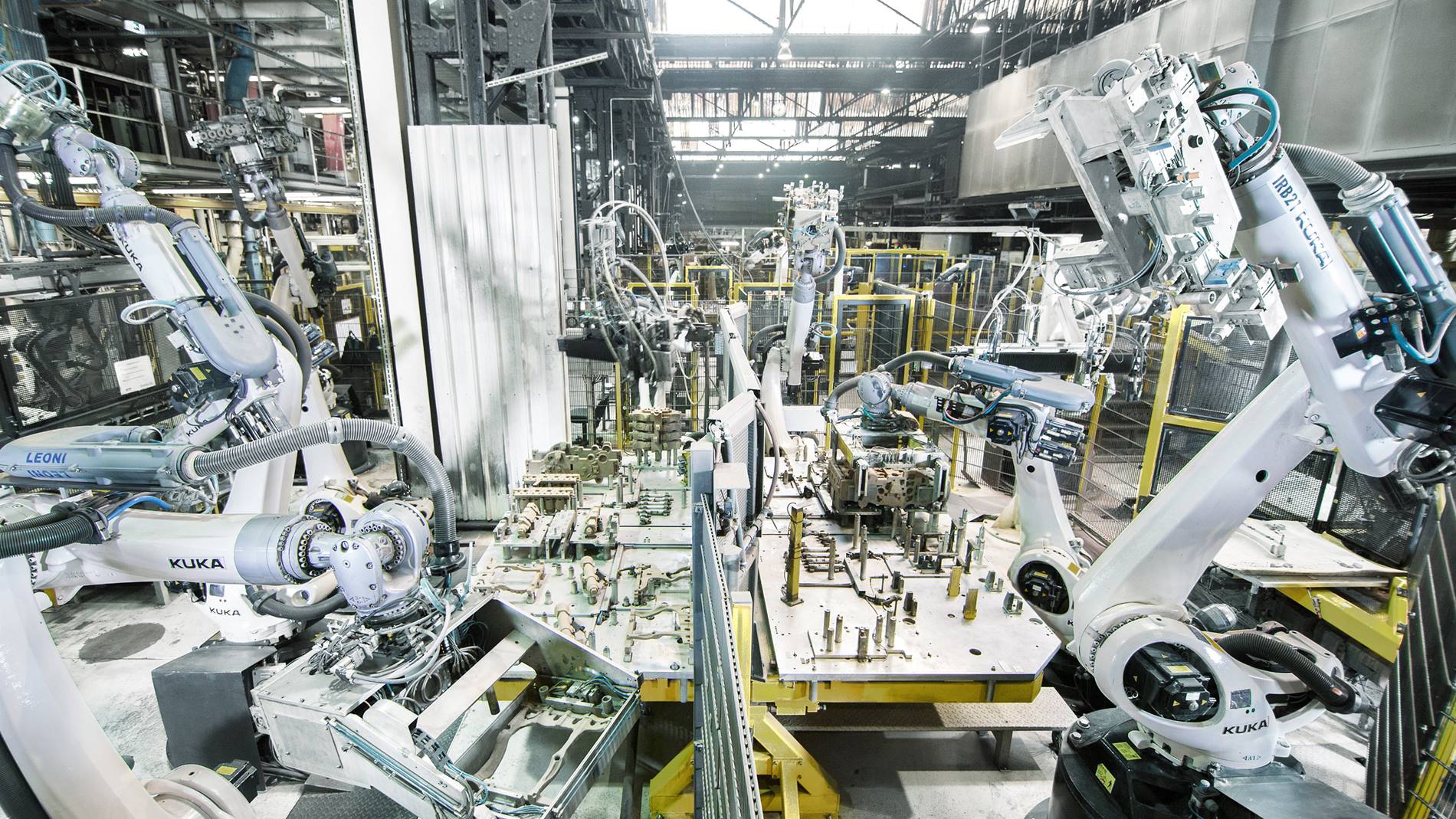
KUKA robots support assembly at NEUE HALBERG GUSS
25 KUKA robots assemble crankcase core packages fully automatically at NEUE HALBERG-GUSS
With 2,250 employees at sites in Saarbrücken and Leipzig, NEUE HALBERG-GUSS GmbH produces and develops cylinder crankcases, cylinder heads for industrial motors made of cast iron and cast crank shafts.
The company is a European market leader and technological pioneer. The product range extends from delicate threecylinder blocks for cars to large-volume V8 units for commercial vehicles. Other products include bearing tunnels made of ductile cast iron and bedplates made of aluminum. Customers include renowned automotive and commercial vehicle manufacturers such as Volkswagen, Daimler, BMW, Audi, MAN, Scania and Iveco.
Fully automated assembly with at most three different robot sizes
The company’s Saarbrücken plant was in search of an automated solution for the complete assembly of crankcase core packages. “As a development partner with experience and expertise, we accompany our customers from product idea to series production readiness. Designing core packages in such a way that they can be assembled fully automatically poses a particular challenge,” explains Peter Koch, project manager at NEUE HALBERG-GUSS.
Here, robot-based automation offers the best solution in terms of flexibility, productivity and quality. For the assembly of crankcase core packages, a maximum of three different robot sizes were to be used.

These had to be ideally suited to the special conditions in a foundry environment and also to allow a particularly space-saving and compact cell concept.
The right KUKA robot for every operation
25 KUKA robots perform all assembly steps fully automatically with utmost precision. The first robots in the assembly process are the KR QUANTEC Foundry robots. They first remove the complete set of cores – consisting of water jacket, balance shafts, channel cores, water pump core, thermostat core, wheel core, crankcase cores and a sole core – from the core shooting machine and set these on the turntables.
The tables then rotate 180 degrees to the smaller KR 5 arc robots. During the subsequent part assembly and deburring “concert”, the flexible KR 5 arc and KR AGILUS robots come into action – positioned overhead, side-mounted on a pedestal and upright. They deburr and assemble the thermostat core and drill holes in the water pump with the utmost precision – and then in the wheel and crankcase, in the water jacket core and in the crank and sole core.
Once both turntables have turned back to the original position, three further KUKA robots from the KR QUANTEC series pick up the individual cores and set them down on the turntable for partial assembly. After another 180-degree turn, two further KR 300 robots set down the completely assembled package.
The next robot removes the package and moves it below the stationary screwfastening station. Following screw fastening, the six-axis robot sets it down on turntable, which then rotates the assembled package towards the washing cell. Once there, a KR 300 picks up the package and immerses it in the wash. By pivoting and rotating the package, it ensures that the wash is applied evenly and then leaves the package to drip. The washed package is then set back down on the turntable and once again rotated 90 degrees towards a manual inspection station.
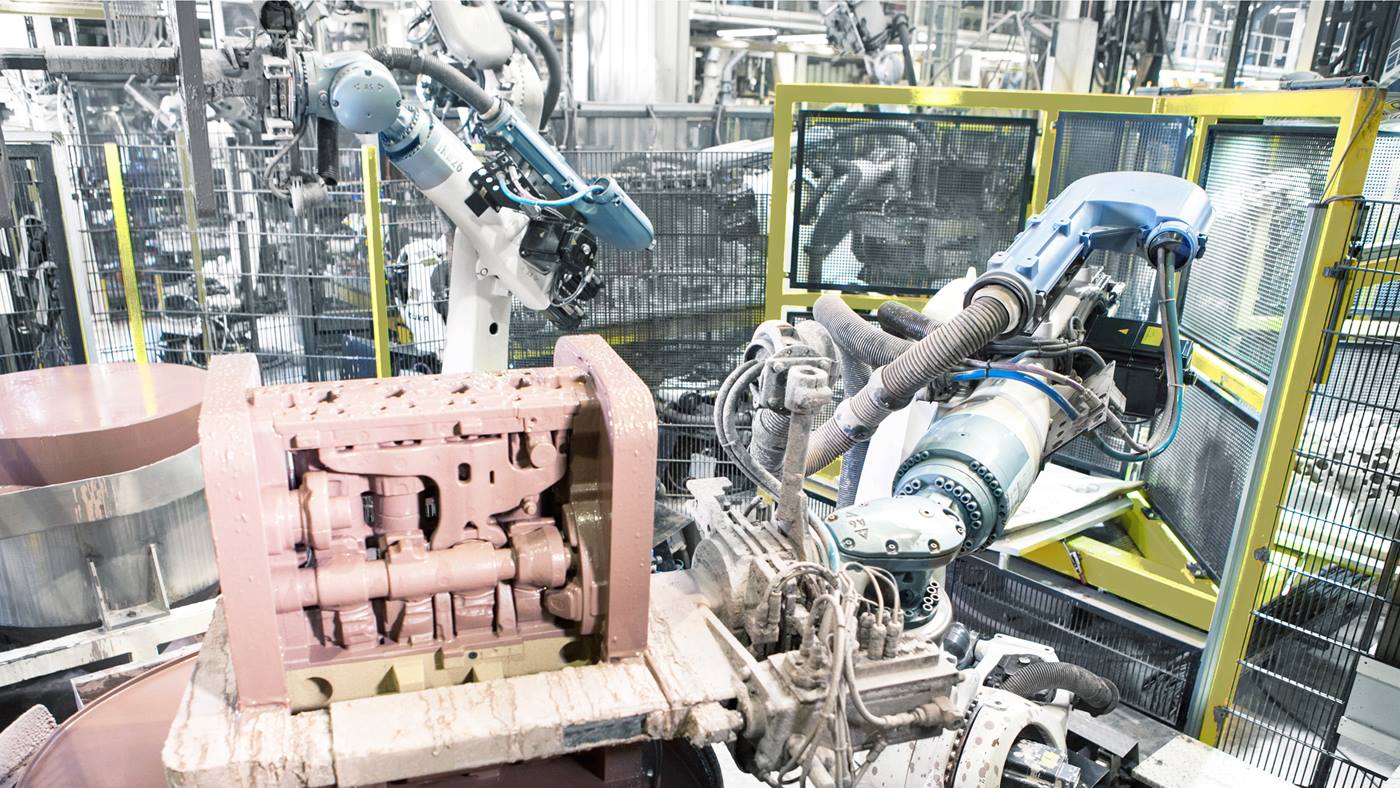
Following approval by the worker, the last robot in the ensemble picks up the core packages and sets them down on a rack with eight slots. Once all of these are filled with wet, washed core packages, the racks are transferred into the drying oven before finding their place among the finished products in the high-bay warehouse.
25 robots harmonize like an orchestra
Thanks to the company’s comprehensive robot portfolio, KUKA is able to offer the optimal solution for both the wide variety of work steps and the interaction of the individual robots. At NEUE HALBERG-GUSS, the 25 robots now work together like an orchestra in perfect harmony. A total of twelve KR 300 R2500 ultra F, eleven KR 5 arc and two KR 6 R900 sixx robots have been assembling crankcase core packages fully automatically since 2013.
With the KR 300 R2500 ultra F robots, NEUE HALBERG-GUSS has opted for veritable foundry experts. The robots of the QUANTEC ultra product family are characterized by high payload capacity combined with maximum performance and the most streamlined design on the market. Their ideal area of use is the handling of heavy workpieces and high-accuracy machining.
In the foundry design, the robots have an impact-resistant, corrosion-protected foundry wrist, which is resistant to both acids and alkalis. It is also protected against dust and dirt and able to withstand temperatures of up to 180 °C for short periods. The KR 5 arc robot and the KR AGILUS stand out in the assembly process thanks to their outstanding precision, flexibility and speed. At the same time, the robot variants from the small robot segment and the low payload range allow particularly space-saving installation in the compact cell concept.
The robot-based system has led to a 50 percent increase in both productivity and quality
High quality at low costs
Today, each system of this robot orchestra assembles around 400 core packages per shift. In addition, production costs have been significantly reduced. The robotbased automation solution also guarantees the Saarbrücken-based company a consistently high quality for the assembled crankcase core packages.
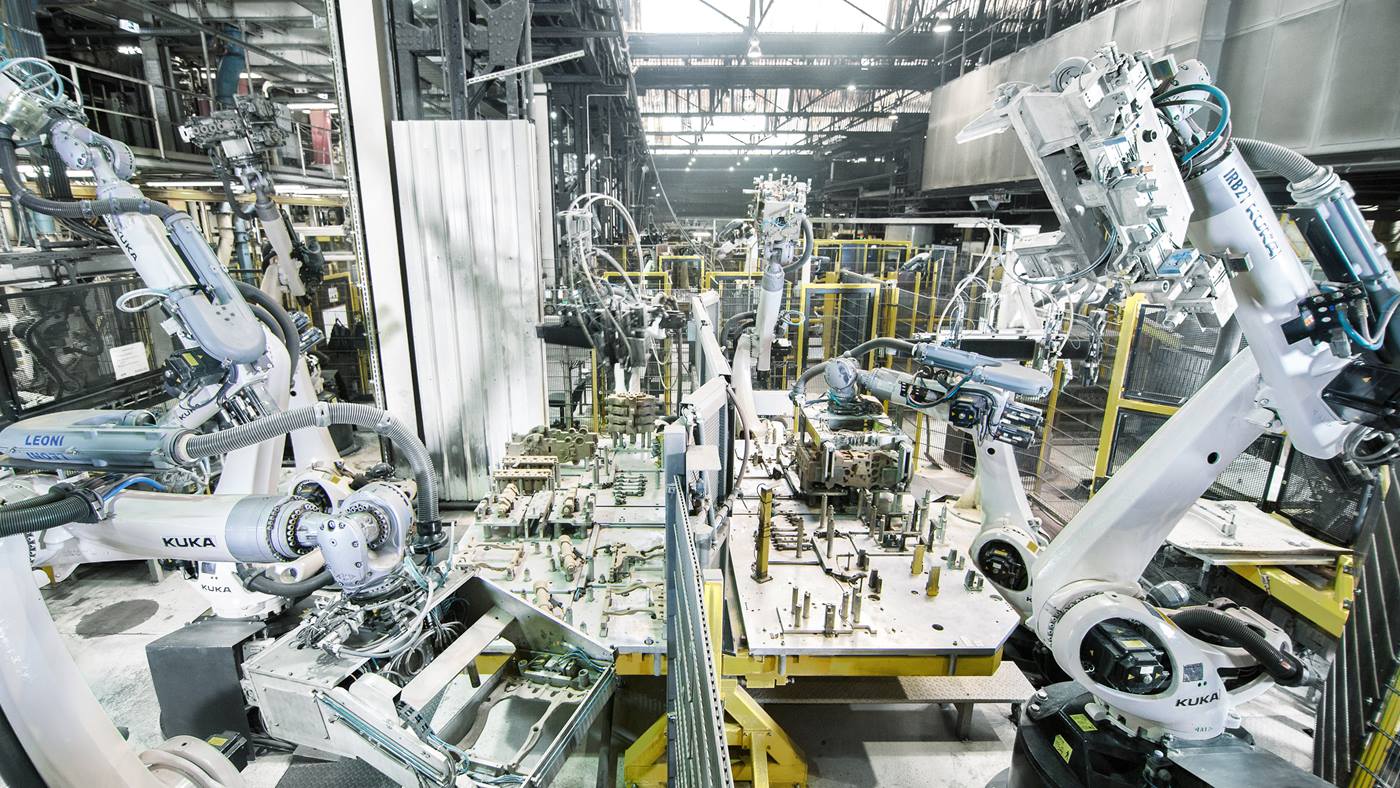
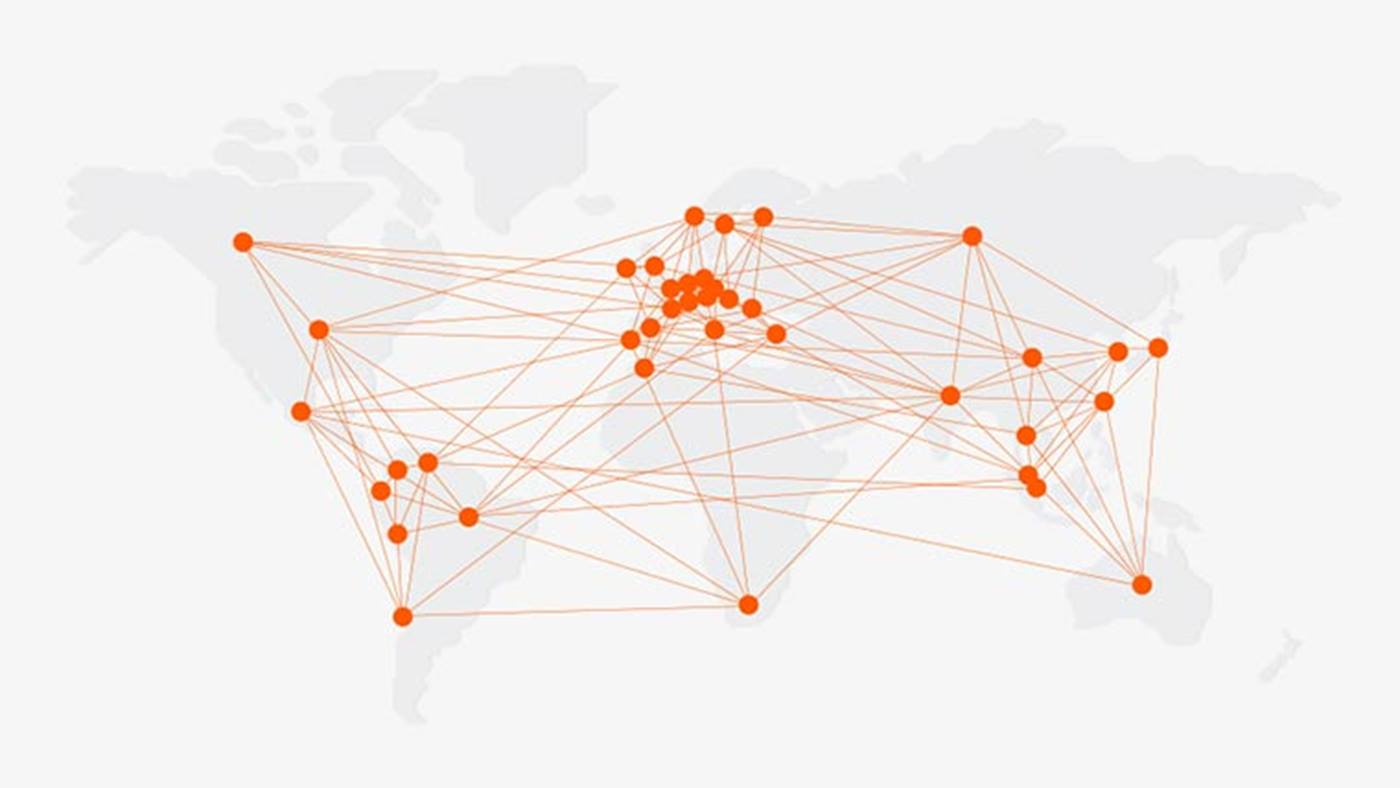
With 2,250 employees at sites in Saarbrücken and Leipzig, NEUE HALBERG-GUSS GmbH produces and develops cylinder crankcases, cylinder heads for industrial motors made of cast iron and cast crank shafts.
The company is a European market leader and technological pioneer. The product range extends from delicate threecylinder blocks for cars to large-volume V8 units for commercial vehicles. Other products include bearing tunnels made of ductile cast iron and bedplates made of aluminum. Customers include renowned automotive and commercial vehicle manufacturers such as Volkswagen, Daimler, BMW, Audi, MAN, Scania and Iveco.
Fully automated assembly with at most three different robot sizes
The company’s Saarbrücken plant was in search of an automated solution for the complete assembly of crankcase core packages. “As a development partner with experience and expertise, we accompany our customers from product idea to series production readiness. Designing core packages in such a way that they can be assembled fully automatically poses a particular challenge,” explains Peter Koch, project manager at NEUE HALBERG-GUSS.
Here, robot-based automation offers the best solution in terms of flexibility, productivity and quality. For the assembly of crankcase core packages, a maximum of three different robot sizes were to be used.

These had to be ideally suited to the special conditions in a foundry environment and also to allow a particularly space-saving and compact cell concept.
The right KUKA robot for every operation
25 KUKA robots perform all assembly steps fully automatically with utmost precision. The first robots in the assembly process are the KR QUANTEC Foundry robots. They first remove the complete set of cores – consisting of water jacket, balance shafts, channel cores, water pump core, thermostat core, wheel core, crankcase cores and a sole core – from the core shooting machine and set these on the turntables.
The tables then rotate 180 degrees to the smaller KR 5 arc robots. During the subsequent part assembly and deburring “concert”, the flexible KR 5 arc and KR AGILUS robots come into action – positioned overhead, side-mounted on a pedestal and upright. They deburr and assemble the thermostat core and drill holes in the water pump with the utmost precision – and then in the wheel and crankcase, in the water jacket core and in the crank and sole core.
Once both turntables have turned back to the original position, three further KUKA robots from the KR QUANTEC series pick up the individual cores and set them down on the turntable for partial assembly. After another 180-degree turn, two further KR 300 robots set down the completely assembled package.
The next robot removes the package and moves it below the stationary screwfastening station. Following screw fastening, the six-axis robot sets it down on turntable, which then rotates the assembled package towards the washing cell. Once there, a KR 300 picks up the package and immerses it in the wash. By pivoting and rotating the package, it ensures that the wash is applied evenly and then leaves the package to drip. The washed package is then set back down on the turntable and once again rotated 90 degrees towards a manual inspection station.
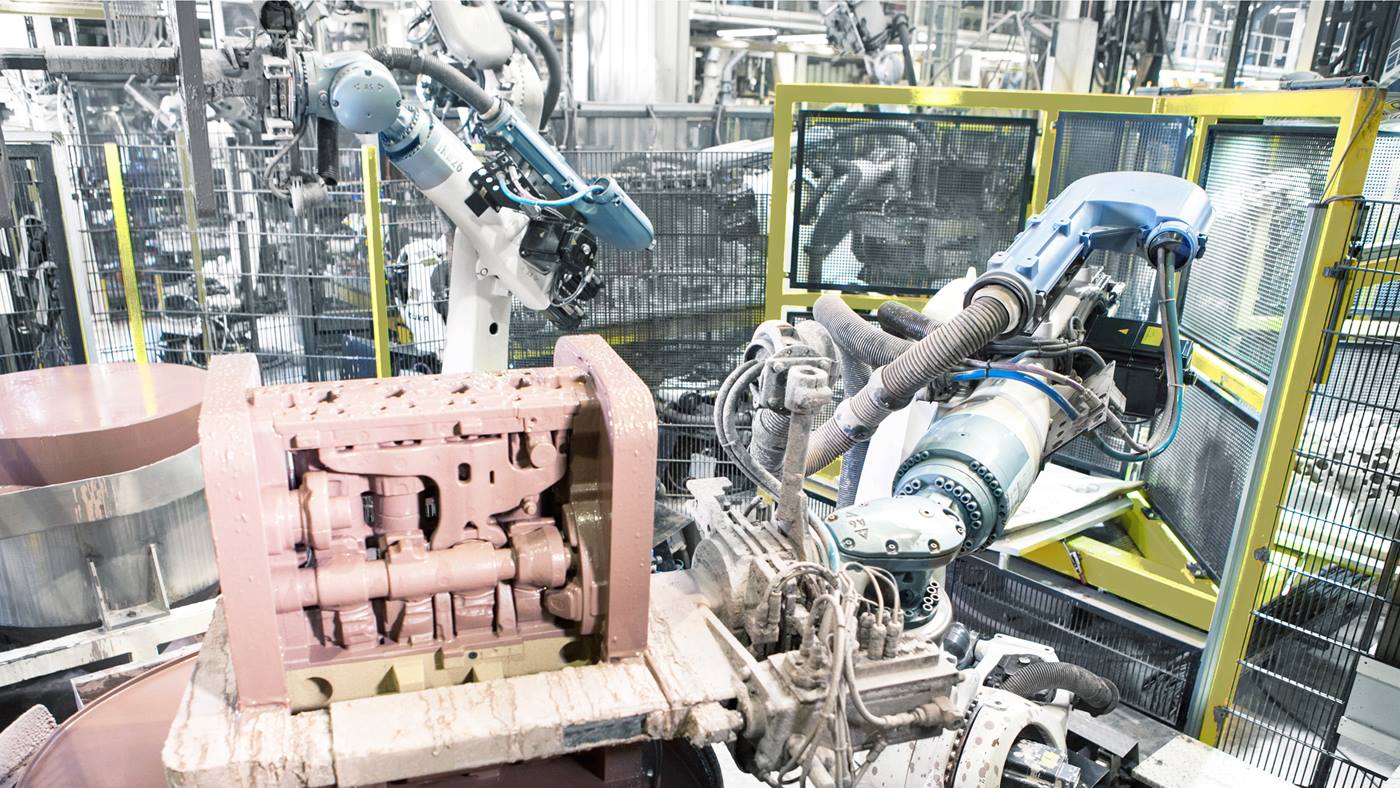
Following approval by the worker, the last robot in the ensemble picks up the core packages and sets them down on a rack with eight slots. Once all of these are filled with wet, washed core packages, the racks are transferred into the drying oven before finding their place among the finished products in the high-bay warehouse.
25 robots harmonize like an orchestra
Thanks to the company’s comprehensive robot portfolio, KUKA is able to offer the optimal solution for both the wide variety of work steps and the interaction of the individual robots. At NEUE HALBERG-GUSS, the 25 robots now work together like an orchestra in perfect harmony. A total of twelve KR 300 R2500 ultra F, eleven KR 5 arc and two KR 6 R900 sixx robots have been assembling crankcase core packages fully automatically since 2013.
With the KR 300 R2500 ultra F robots, NEUE HALBERG-GUSS has opted for veritable foundry experts. The robots of the QUANTEC ultra product family are characterized by high payload capacity combined with maximum performance and the most streamlined design on the market. Their ideal area of use is the handling of heavy workpieces and high-accuracy machining.
In the foundry design, the robots have an impact-resistant, corrosion-protected foundry wrist, which is resistant to both acids and alkalis. It is also protected against dust and dirt and able to withstand temperatures of up to 180 °C for short periods. The KR 5 arc robot and the KR AGILUS stand out in the assembly process thanks to their outstanding precision, flexibility and speed. At the same time, the robot variants from the small robot segment and the low payload range allow particularly space-saving installation in the compact cell concept.
The robot-based system has led to a 50 percent increase in both productivity and quality
High quality at low costs
Today, each system of this robot orchestra assembles around 400 core packages per shift. In addition, production costs have been significantly reduced. The robotbased automation solution also guarantees the Saarbrücken-based company a consistently high quality for the assembled crankcase core packages.
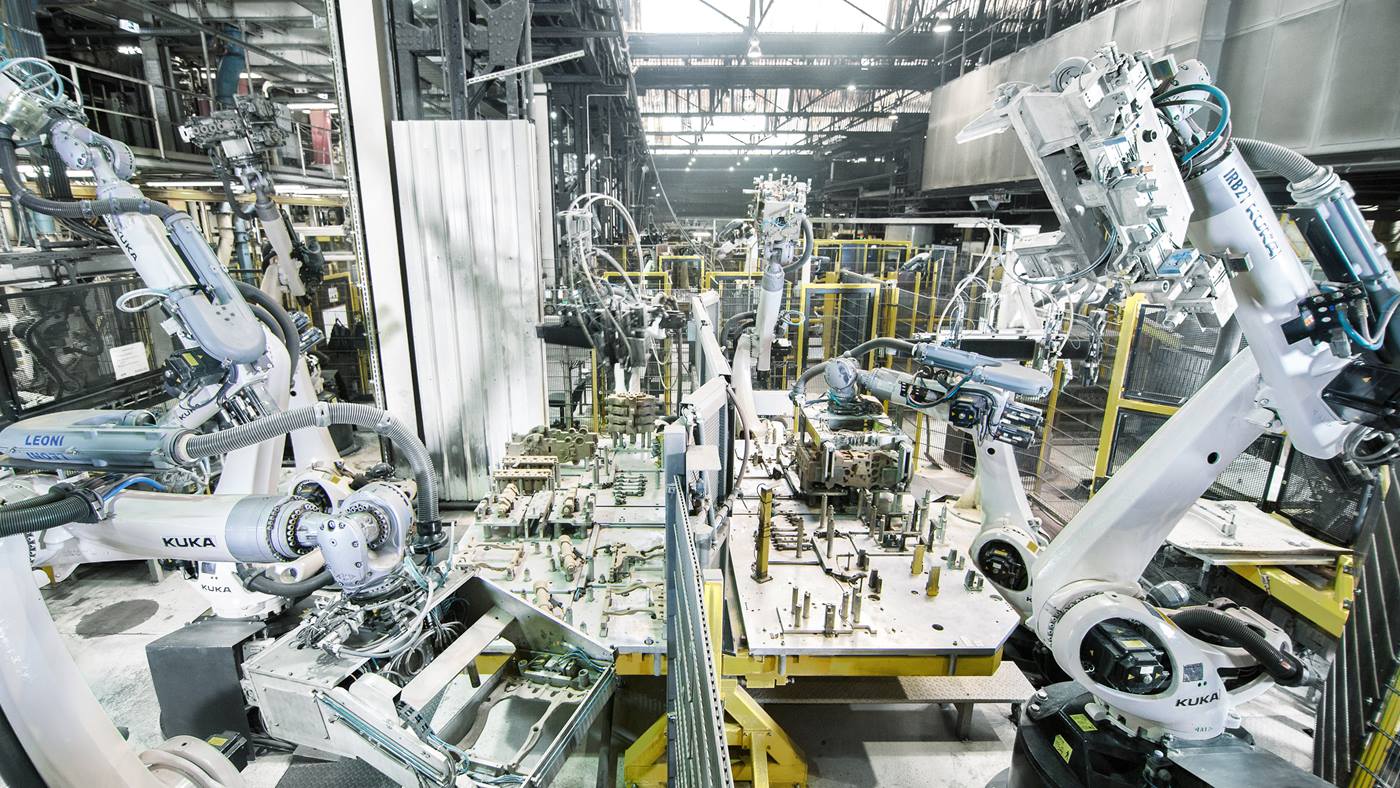