Jubiläum bei KUKA: 50 Jahre Reibschweißen
Hintergrundbericht zum Thema „Reibschweißen“
15. November 2016
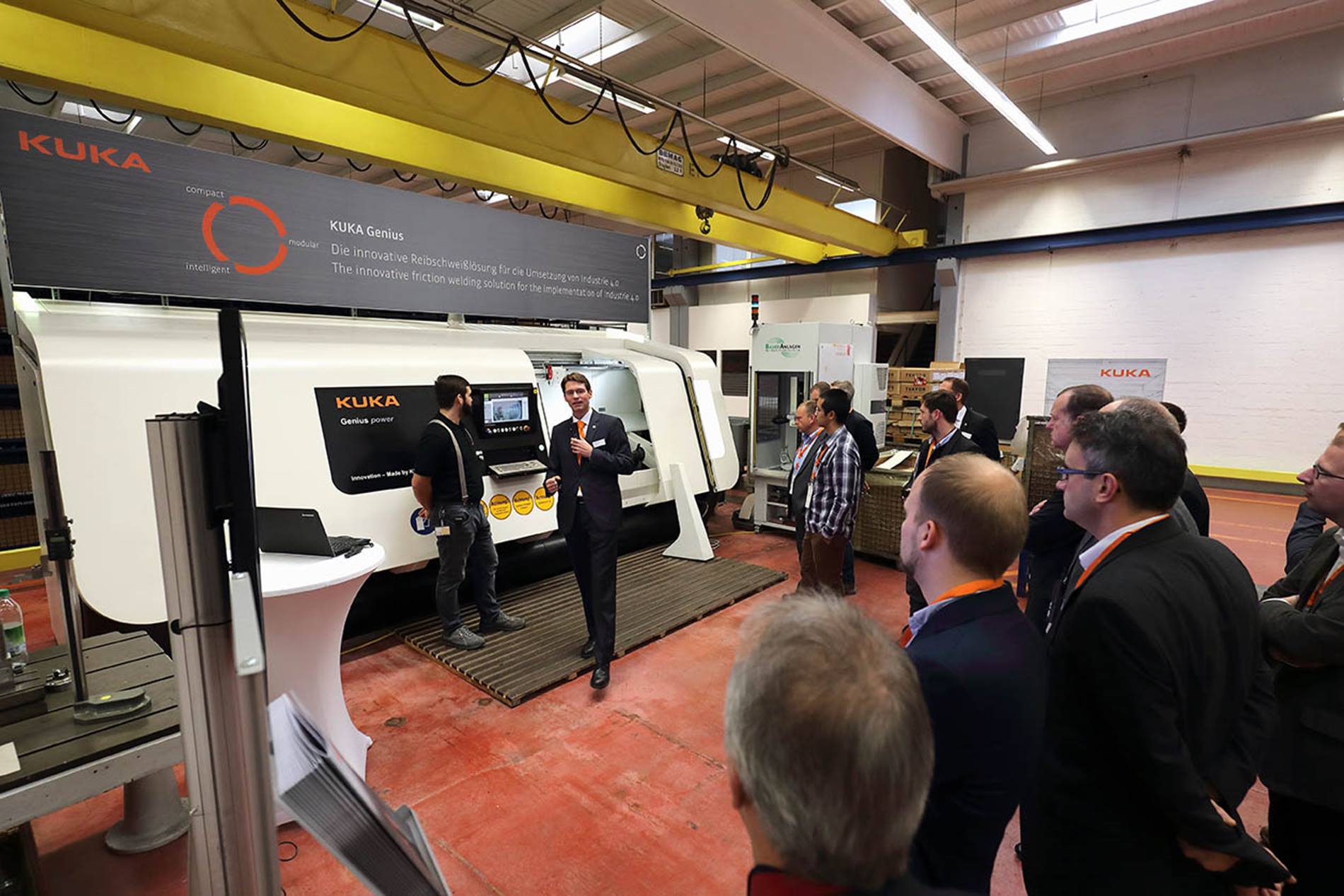
„Reibschweißen, ein Verfahren mit Zukunft“ – Schon im Jahre 1966 warb KUKA mit dem Slogan und sollte damit Recht behalten. Schnell, sicher und wirtschaftlich: Charakteristika, die das Verfahren auszeichnen und bis heute unverzichtbar machen. Vor allem die Kombination unterschiedlicher Werkstoffe sprechen für die Technologie. KUKA erkannte die Vorteile des Reibschweißens schon sehr früh und entwickelte den Prozess über die Jahre weiter. Heute kann das Augsburger Unternehmen auf eine 50-jährige Erfolgsgeschichte zurückblicken.
Reibschweißen 4.0: Alles andere als verstaubt
„Oft wirkt der Begriff Reibschweißen etwas verstaubt“, sagt Walter Weh, Division Head Advanced Welding Solutions von KUKA Industries. „Die Technologie ist das aber auf keinen Fall.“ Seit fünf Jahrzehnten entwickeln und verbessern die KUKA Experten den Prozess. Von der ersten Doppelkopfmaschine für Gelenkwellen für Daimler in den 1970er Jahren bis zur modularen Reibschweißmaschine KUKA Genius. „Wir orientieren uns an den Marktbedürfnissen, gehen mit der Zeit und können durch unsere jahrelange Erfahrung und Expertise im Reibschweißen für jeden Kunden die passende Lösung finden“, sagt Weh.
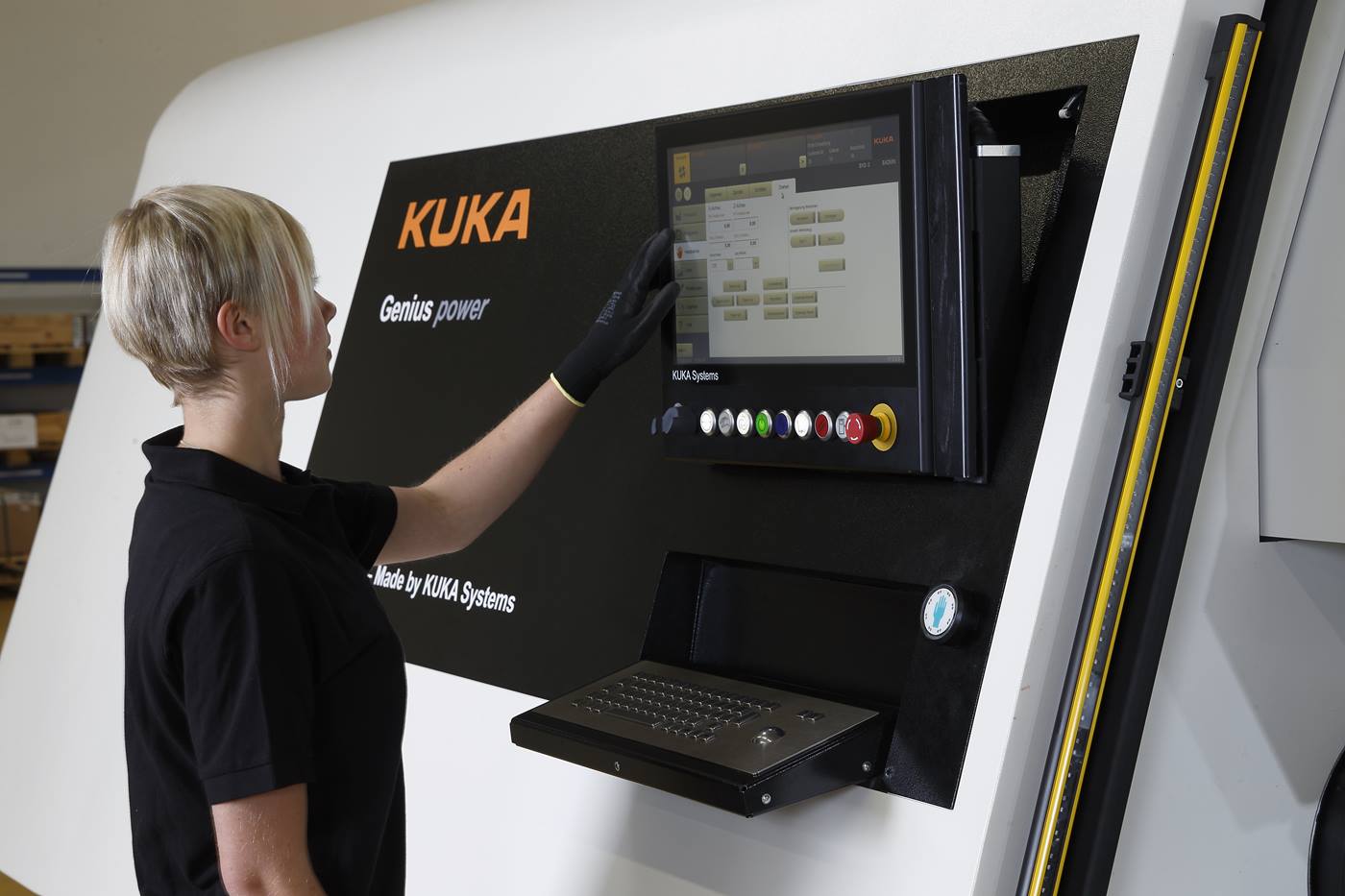
Der Automationsspezialist KUKA Industries hat Industrie 4.0 frühzeitig in den Reibschweißmaschinen berücksichtigt, um seinen Kunden Lösungen für nachhaltige Produktivitätserhöhungen zu bieten. Mit einer vollständigen Integration der Reibschweißmaschine in das Produktionsnetz, lässt sich eine höhere Produktivität erreichen. Dank dieser digital vernetzten Prozesse wird es möglich Produkte flexibler, energieeffizienter, ressourcenschondend und individueller herzustellen.
Alle Prozessdaten werden von der KUKA PCD (Process Control and Documentation)-Steuerung numerisch überwacht und elektronisch archiviert und stehen daher für weitere Analysemöglichkeiten z.B. in Cloud-Systemen zur Verfügung. Das ist die Basis für die Umsetzung von Industrie 4.0 und schafft somit nachvollziehbare Qualität und Datentransparenz.
Der sichere Umgang mit großen Datenmengen spielt dabei eine grundlegende Rolle, ebenso wie einheitliche Standards an den Schnittstellen der Systeme. Anwendbar ist dieses Prinzip nicht nur bei neuen Produkten und Lösungen. Auch Roboter, Zellen und Anlagen, die bereits im Einsatz sind, können auf diese Art verbunden werden.
1966: KUKA etabliert das Reibschweißen – ein geschichtlicher Rückblick
Schon unsere steinzeitlichen Vorfahren wussten, dass man durch Reibung Wärme erzeugen kann. Das gleiche Prinzip steckt auch hinter der Technologie des Reibschweißens. Dabei wird eine Komponente fixiert, während das andere Werkstück in Rotation versetzt wird und sich mit einer Relativbewegung dem fest eingespannten Teil nähert. Die Kontaktflächen berühren sich und das Material plastifiziert. Unter hohem Druck werden die beiden Teile aufeinandergepresst und schließlich verbunden.
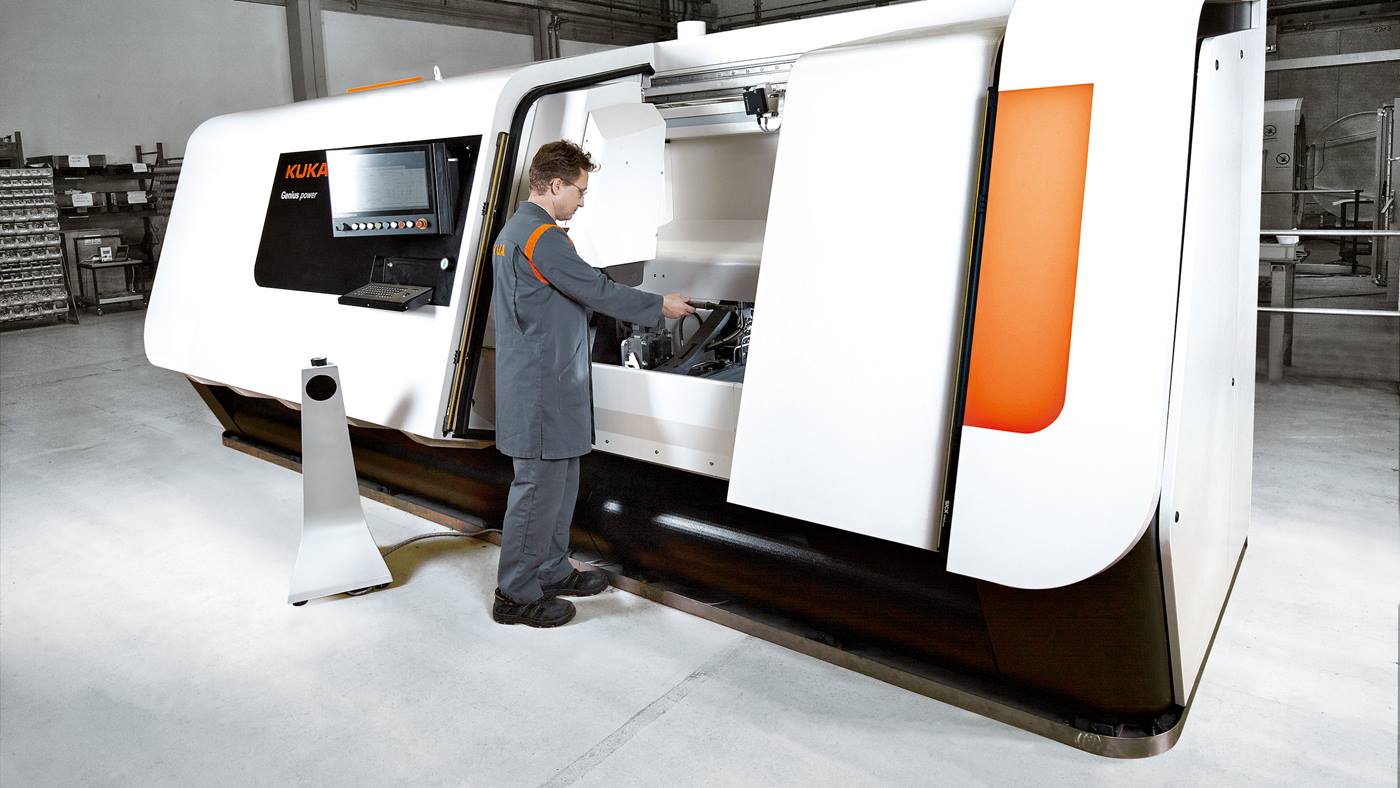
Erste Patente zum Erwärmen und Schweißen gab es bereits Ende des 19. Jahrhunderts. Die erste funktionstüchtige Maschine wurde 1958 in der Sowjetunion entwickelt und gebaut. 1966 brachte KUKA die erste Maschine auf den Markt. Zahlreiche KUKA Innovationen prägen seitdem diesen Bereich: So folgte 1970 bereits eine Reibschweißmaschine mit Hybrid-Antrieb, einer Kombination aus dem kontinuierlichen Fremdantrieb und dem Schwungradreibschweißen.
„Aufgrund sehr hochwertiger Spindellagerungen und exakt wirkender externer Bremssysteme konnte KUKA lange Zeit, als einziger Hersteller, beliebige Brems- und Stauchzeitpunkte frei vorgeben“, erinnert sich Gerhard Hauswurz, Global Sales Manager von KUKA Industries. Mit der Übernahme des großbritannischen Wettbewerbers Thompson konnte das Produktportfolio noch weiter ausgebaut werden.
Heute können die Kunden aus einer Palette von Maschinen mit unterschiedlichem Anpressdruck von zwei bis 1.000 Tonnen auswählen. Mit der KUKA Genius im Jahr 2015 präsentierte der Automatisierungsspezialist die neueste Reibschweißgeneration: flexibel, energieeffizient und leistungsstark ist die kompakte und modulare Maschine. Zudem doppelt preisgekrönt durch den Red Dot Design Award 2015 und den German Design Award 2016. Sie glänzt also auch durch ihre Optik.
Fakten zum KUKA Reibschweißen
KUKA installierte über 1.000 Anlagen in 44 Ländern.
- Der Heiz-/Glühstab für Dieselmotoren ist das kleinste geschweißte Bauteil mit einem Durchmesser von 3 Millimeter.
- Der Druckzylinder mit 700 Kilogramm war das schwerste geschweißte Bauteil.
- Vor über 25 Jahren entwickelte Rainer Simanowski, der heutige Leiter Technology Services von KUKA Industries, im Rahmen seiner Diplomarbeit eine Tisch-Reibschweißmaschine, die zu Vorführungszwecken zum Kunden mitgenommen werden konnte.
- Die Tisch-Reibschweißmaschine, die eine Größe von ca. drei Schuhkartons hatte, wurde in der „Knoff-Hoff-Show“, einer damaligen ZDF-Wissenschaftssendung, einem Millionenpublikum präsentiert.
Auftragsfertigung im KUKA Maschinenpark
- Seit 1970 – seit fast 50 Jahren – bearbeitet KUKA Lohnaufträge für namhafte Unternehmen.
- Neben der Reibschweißtechnologie können auch weitere Verfahren wie das Magnetarc- oder Laserschweißen im KUKA Maschinenpark durchgeführt werden.
- Der KUKA Maschinenpark hat eine Produktionsfläche von 2.000 Quadratmetern:
- zehn Maschinen unterschiedlicher Leistungsklassen für das Rotationsreibschweißen mit Querschnitten von drei bis 31.400 Quadratmillimetern und einer Stauchkraft von 1 bis 300 Tonnen
- zwei Maschinen für das Magnetarc-Schweißen mit Querschnitten von 60 bis 4.000 Quadratmillimetern und einer Stauchkraft von 1 bis 35 Tonnen
- vier flexible Roboterzellen für die Laserbearbeitung mit bis zu acht Kilowatt Laserleistung und verschiedenen Bearbeitungsoptiken für das Dünn- und Dickblechschweißen
- Von der Prozessvalidierung bis hin zur Prototypenfertigung profitieren Kunden von der langjährigen KUKA Expertise.
- zehn Maschinen unterschiedlicher Leistungsklassen für das Rotationsreibschweißen mit Querschnitten von drei bis 31.400 Quadratmillimetern und einer Stauchkraft von 1 bis 300 Tonnen