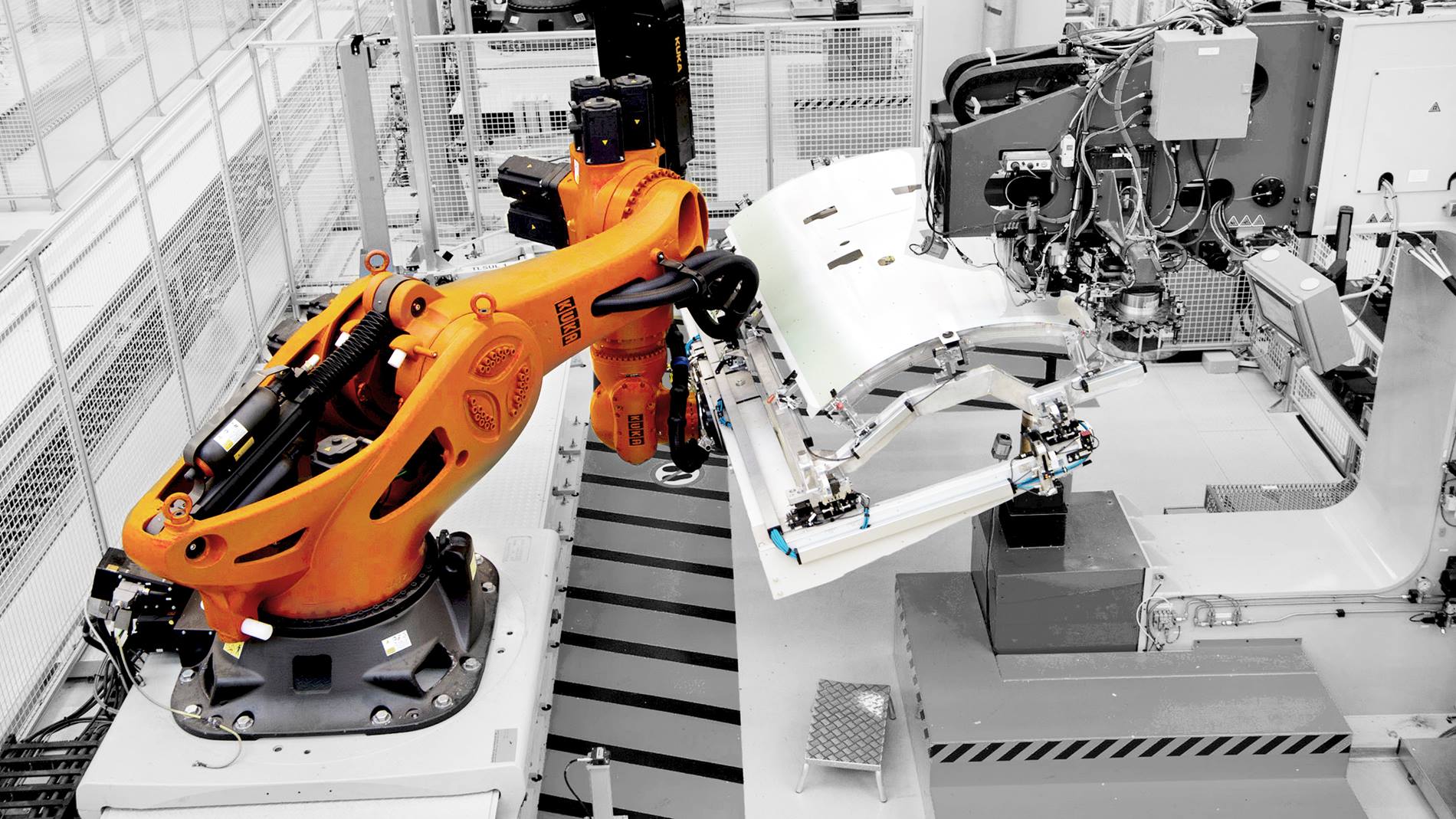
Premium AEROTEC produziert Rumpfsektion für Airbus noch schneller, günstiger und transparenter
Premium AEROTEC ist auf Design und Produktion großer und komplex geformter Flugzeugbauteile spezialisiert – wie die Rumpfsektion 19 für die Airbus-320-Familie. Um die Stückzahlen zu erhöhen und gleichzeitig die Herstellungskosten zu senken, baut Premium AEROTEC auf eine speziell für den Aerospace-Bereich entwickelte KUKA Anlage. Damit steht in Augsburg jetzt die modernste Flugzeugmontagelinie der Welt.
Die Aufgabe: Intelligent vernetzte Automation
Die Lösung: Alles aus einer Hand mit KUKA
Die Teilschalen durchlaufen eine 80 Meter lange Produktionsanlage von KUKA. In manuellen und automatisierten Schritten werden sie vernietet und zu Halbsektionen vormontiert. Bis zu 50 Sektionen können pro Monat gefertigt werden.
Zum Einsatz kommen drei KUKA KR 1000 titan Handling-Roboter und drei „All Electric Bohr-/Nietautomaten“. Diese wurden komplett von KUKA realisiert – unter anderem in Zusammenarbeit mit deren Unterlieferanten, wie der US-Amerikanischen Firma Gemcor.

Gut zwei Jahre arbeitete KUKA – hier in der Rolle des Anlagenintegrators – mit den Verantwortlichen bei Premium AEROTEC und weiteren Partnern an dem Projekt. KUKA übernahm federführend Planung und Entwicklung, fertigte und beschaffte alle Komponenten und Anlagenteile, integrierte Steuerungssysteme, koordinierte alle Unterlieferanten und sorgte dafür, dass die Anlage pünktlich aufgebaut und in Betrieb genommen wurde.
Auf dem Weg zu Industrie 4.0 mit einer transparenten Produktion
Zu Beginn des Fertigungsablaufs erhält jede Teilschale einen RFID-Chip. Anhand dieses Chips können die Handling-Roboter und Nietanlagen an den einzelnen Stationen erkennen, um welches Bauteil es sich handelt und z. B. zum entsprechenden Werkzeug wechseln. Jedes Bauteil lässt sich so über den gesamten Fertigungsprozess lückenlos verfolgen – für eine transparente Produktion, ganz im Sinne der Industrie 4.0.
Innovativer Leichtbau-Bauteilträger
Bislang kamen als Bauteilträger bis zu 1.000 Kilogramm schwere Modulpaletten aus Stahl zum Einsatz. Zusammen mit Premium AEROTEC entwickelte KUKA eine Aluminium-Leichtbau-Konstruktion als Greifer am Roboter und einen Bauteilträger, der samt Teilschale nur noch rund 400 Kilogramm wiegt. Die Last lässt sich so schnell und präzise bewegen, was die Fertigungs- und Montagekosten deutlich verringert.
Integration verschiedener Steuerungen
Als übergeordnete Maschinensteuerung integrierte KUKA die Siemens Sinumerik 840D. KUKA definierte und implementierte auch die Schnittstelle zwischen der Siemens-Steuerung und der KUKA Robotersteuerung KRC4. Die Werker können so alle Maschinen über eine einzige, vertraute Oberfläche bedienen. Dabei spielt es keine Rolle, ob es sich um KUKA Handling-Roboter handelt oder die Maschinen Dritter – wie die US-Amerikanischen Nietautomaten, die KUKA nahtlos in die Anlage eingebunden hat. Mit dem KUKA eigenen Steuerungsstandard miKUKA werden Informationen gesammelt, an der Linie visualisiert und den Kundensystemen zur Verfügung gestellt. Die Roboterbewegung für den Bohr-/Nietprozess wurde komplett offline programmiert.
Die Vorteile der Automations-Lösung:
-
Geringere Wartezeiten und Durchlaufzeit
-
Verringerter Logistikaufwand
-
Transparente Produktionsabläufe
-
Ergonomischere manuelle Arbeitsschritte
-
Höchste Genauigkeit und Produktivität bei gleichzeitig attraktiven Kosten
Mit dem KUKA Lösungsportfolio, kombiniert mit unserem tiefen Fachwissen in der Flugzeugmontage, konnten wir die Verfügbarkeit und die Performance unserer Produktion optimieren.
