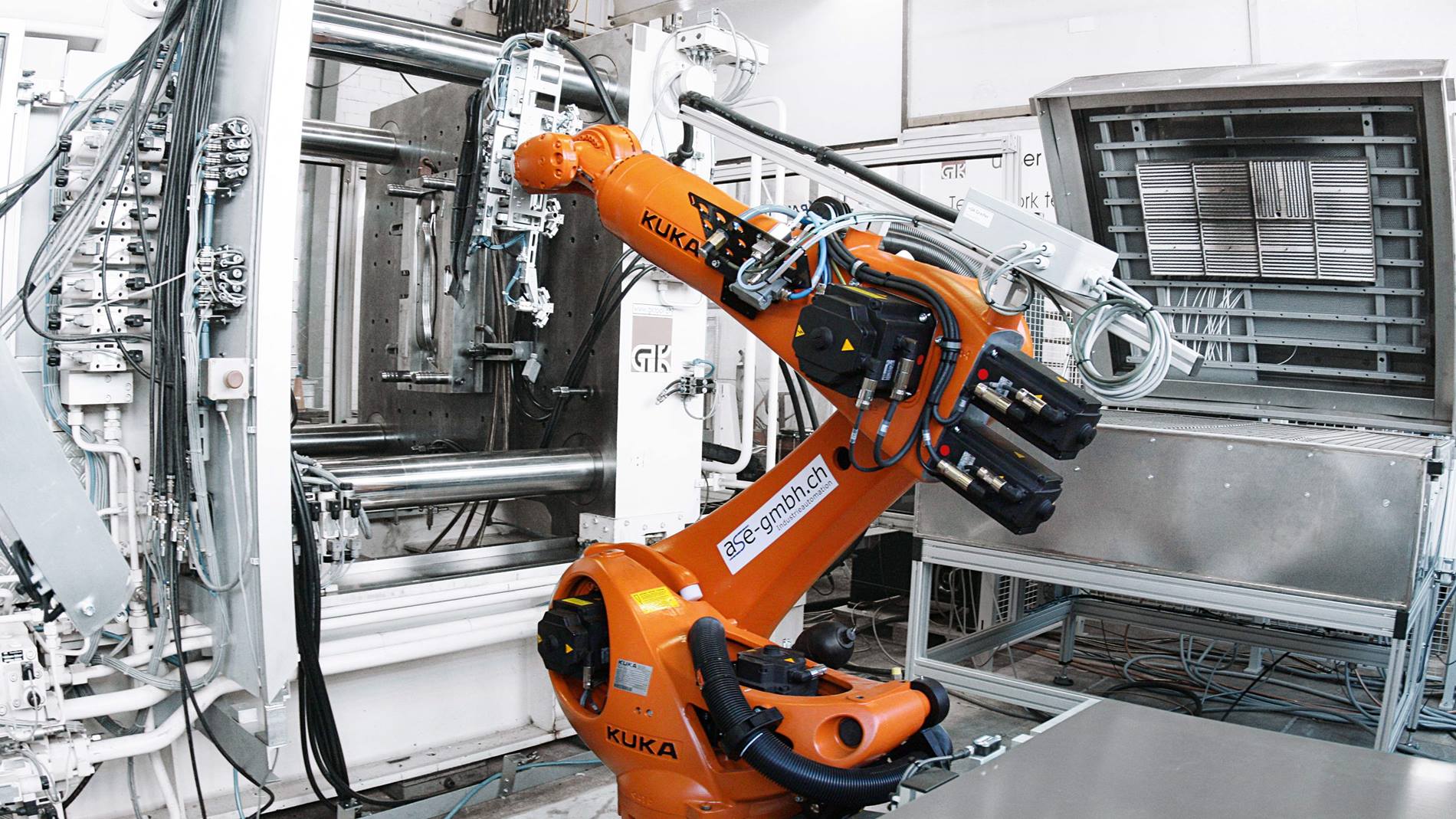
KUKA uses two machine tools to manufacture 14 different components – for and with KUKA robots
KUKA Roboter GmbH, with its headquarters in Augsburg, is one of the global market leaders in the development, production and sale of industrial robots, controllers and software.
The company also relies on automation for its own robot production. The latest robotic automation of two machining centers in Hall 10 has resulted in an average increase in productivity of more than 15 percent.
Components for the production of KUKA robots
In an area covering 3000 square meters, the machining operations department housed here manufactures components that are used for the production of KUKA robots. Since 2013, DMG MORI machine tools of type Sprint 65-3 (Sprint for short) and CTX beta 1250 TC-4A (CTX for short) have been manufacturing 14 components from castings and sawn sections that are then installed in the adjacent robot assembly shop.
Highly flexible automation solution
This automation solution is characterized by its high degree of flexibility in the smallest of spaces. Use of the KS CycleMove workpiece feed system from KUKA Systems GmbH makes the cells even more adaptable. Furthermore, buffering of the components enables a maximum unmanned operating time of eight hours. While the Sprint system – an automatic lathe – manufactures robot components from sawn sections within a few minutes, the neighboring CTX automatic milling lathe performs machining operations on castings and sawn sections with a cycle time of approx. 30 minutes.
A total of seven components are currently manufactured on the Sprint, ranging from a pin for the KR QUANTEC series with a diameter of 55 mm to a flange for the heavy-duty robots of the KR FORTEC series with a diameter of 120 mm. The CTX also manufactures seven components, with parts being machined to produce, for example, spur gear housings for the KR AGILUS and KR QUANTEC, with diameters ranging from 95mm to 246 mm. With the aid of several supply and return conveyors, the machining centers can work autonomously in three-shift operation.
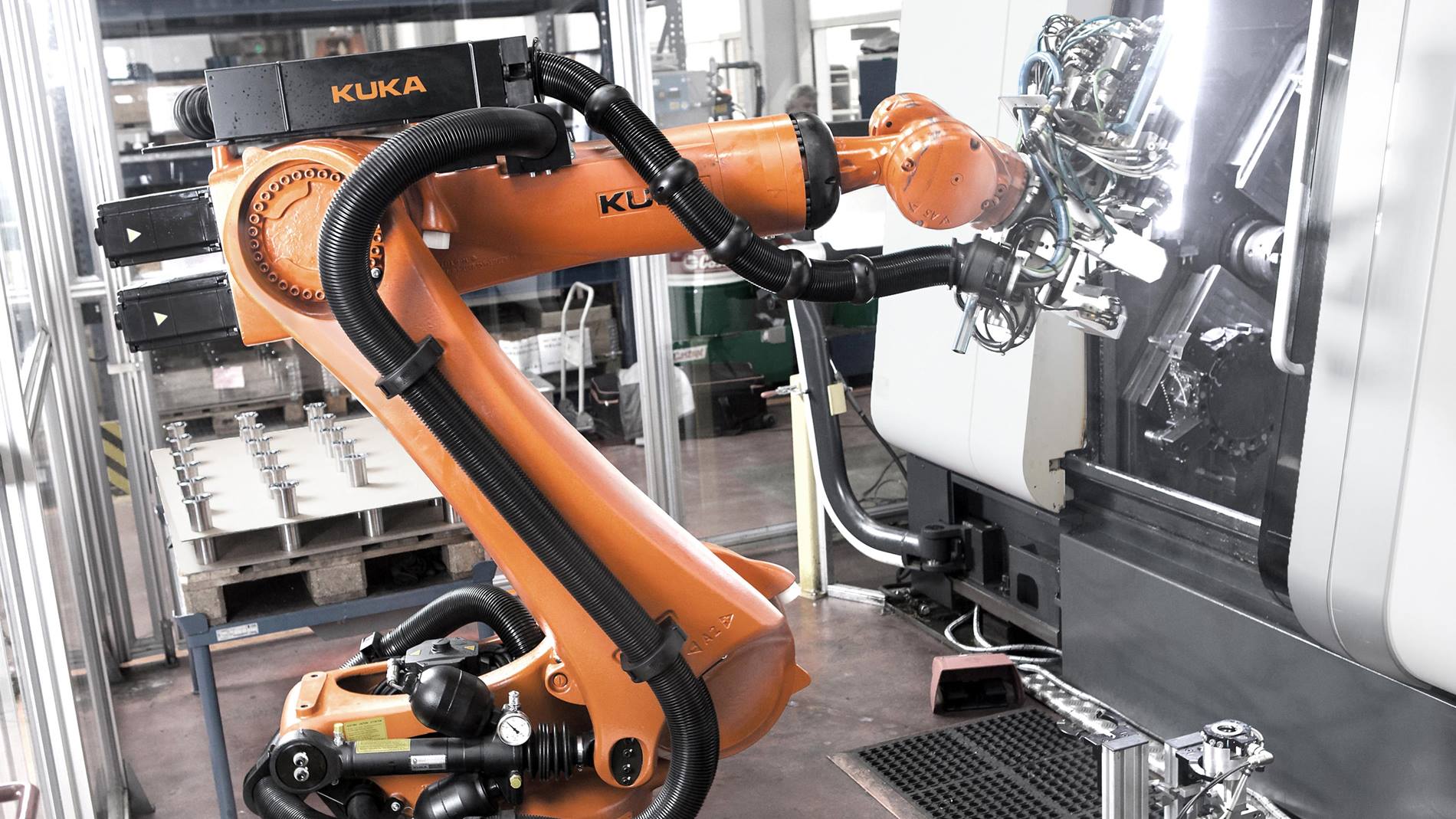
Minimum changeover work and expandability
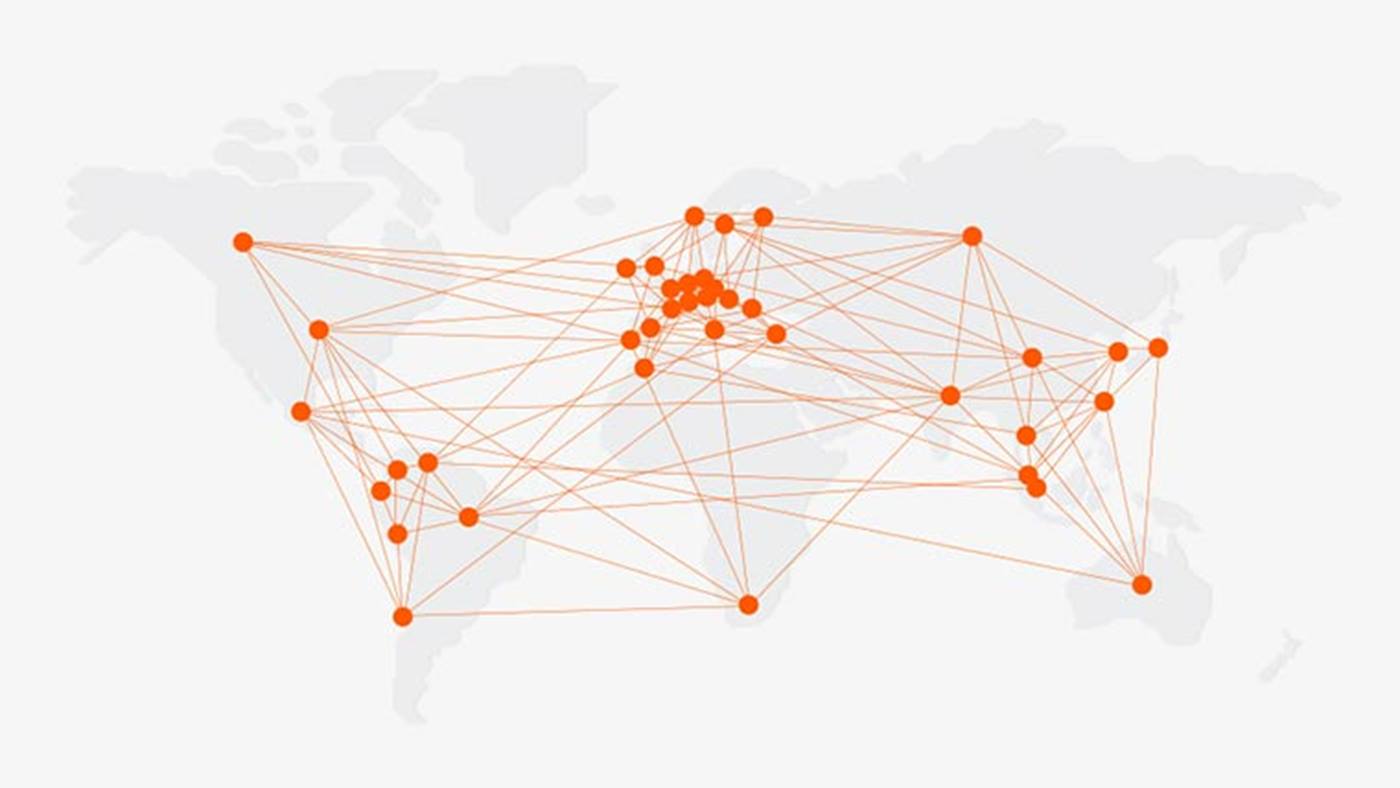