
Quick stacking: KUKA robots palletise water bottles
Three different KUKA palletizers stack water bottles on pallets - layer by layer - at a water factory in Ramah, Saudi Arabia. Quickly and precisely. This works primarily thanks to the integrated KUKA software solutions.
“Automation was the logical approach for us”

Palletizers perform precise preparatory work on the conveyor


Easy changing of setdown formations

Playing for high stacks: KR 700 PA scores highly in terms of reach

One of the fastest lines in the beverage industry

Thanks to the KUKA.PLC mxAutomation software, the formation of the water bottles in each pallet layer can be modified by means of a simple setting on the system controller.
Increased productivity of the system, lower costs
Additionally, the automated solution makes it possible to process several different beverage bottles simultaneously – for continuous production and greater flexibility at times of high demand. Due to the short changeover times, achieved by simply touching the user interface, the company achieves further time savings. This results in a lower total cost of ownership and increased product quality. The gentle handling of the bottles and packages during automatic sorting, bundling and stacking ensures minimized deformation or damage to the goods.
“Our customer is highly satisfied with the solution we developed using KUKA technologies,” confirms Bashir Alqatanani. “In particular, the simple changeover of layer configurations thanks to KUKA.PLC mxAutomation has convinced the employees.” Integrator MEMCO intends to carry on working on the palletizing line, however, and make it even faster. It will continue to rely on KUKA solutions in the future.
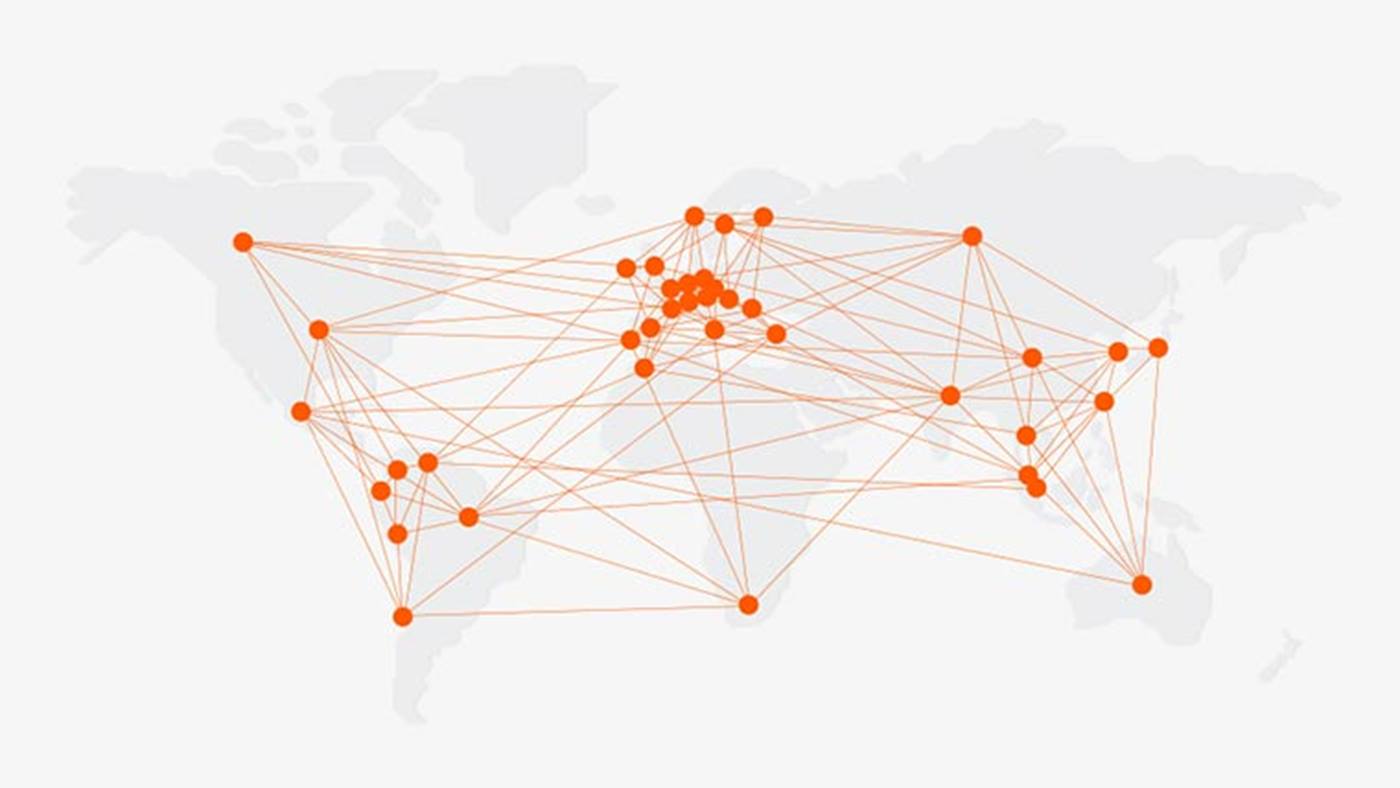