
MRK-Lösung entlastet Mitarbeiter bei Qualitätssicherung
Die MRK-Systeme GmbH hat sich auf Mensch-Roboter-kooperierende Industrielösungen spezialisiert. Für die BMW Group hat das Unternehmen für die Qualitätssicherung der Kurbelwellengehäuse eine MRK-fähige Automatisierungslösung mit KUKA Robotern der KR QUANTEC Serie entwickelt.
Das BMW Group Werk Landshut unterhält eine der modernsten Leichtmetallgießereien der Welt. Ob Drei-, Vier-, oder Sechszylinder Motoren, für sämtliche Modelle der BMW-Flotte werden hier die Kurbelwellengehäuse gefertigt. Die Qualitätssicherung der Kurbelwellengehäuse kann zwar nicht vollständig automatisiert werden, da es weiterhin des geschulten Blicks der Mitarbeiter bedarf. Die Wahl fiel auf eine Anlage, in der Mensch und Roboter direkt zusammenarbeiten. Das Unternehmen MRK-Systeme wurde dafür mit der Umsetzung betraut. „Die Mensch-Roboter-Kollaboration sorgt für die ergonomische Entlastung der Mitarbeiter von BMW“, erklärt Michael Mohre, verantwortlich für den Bereich Operations bei der MRK-Systeme GmbH. Seit nunmehr eineinhalb Jahren stehen zwei identische Applikationen mit jeweils einem KUKA Roboter aus der KR QUANTEC Serie vom Typ KR 210 R2900 prime K - der Konsolen-Ausführung - an der Produktionslinie in Landshut. Jeweils ein Mitarbeiter steuert dabei mittels Joystick die Bewegungen des Roboters, um in einer angenehmen Körperhaltung die Bauteile auf Fehler zu prüfen.
Roboterbedienung unterstützt den Prüfvorgang
Über ein Förderband werden alle produzierten Kurbelwellengehäuse in den Arbeitsbereich angeliefert. Je nach Bauart wählt die überlagerte Robotersteuerung das entsprechende Programm zur Bewegungsbedienung des Roboters aus. Der Werker steuert mittels Joystick dessen Bewegungen. Der Roboter bewegt sich dabei auf einer vorgegebenen Bahn zu dem Gehäuse, schließt den Greifer und reicht das Bauteil dem Werker, der mittels Kaltlichtlampe das Kurbelgehäuse auf Fehler prüft. Währenddessen hält der Roboter das rund 30 kg schwere Bauteil sicher in der für den Mitarbeiter optimalen Höhe. Hat der Werker den Prüfvorgang abgeschlossen, fährt er den Roboter samt Gehäuse zurück zum Förderband und legt es ab. Beendet ist der interaktive Prüfvorgang mit einem Knopfdruck, damit dokumentiert der Mitarbeiter, ob das Bauteil „in Ordnung“ oder „nicht in Ordnung“ ist.
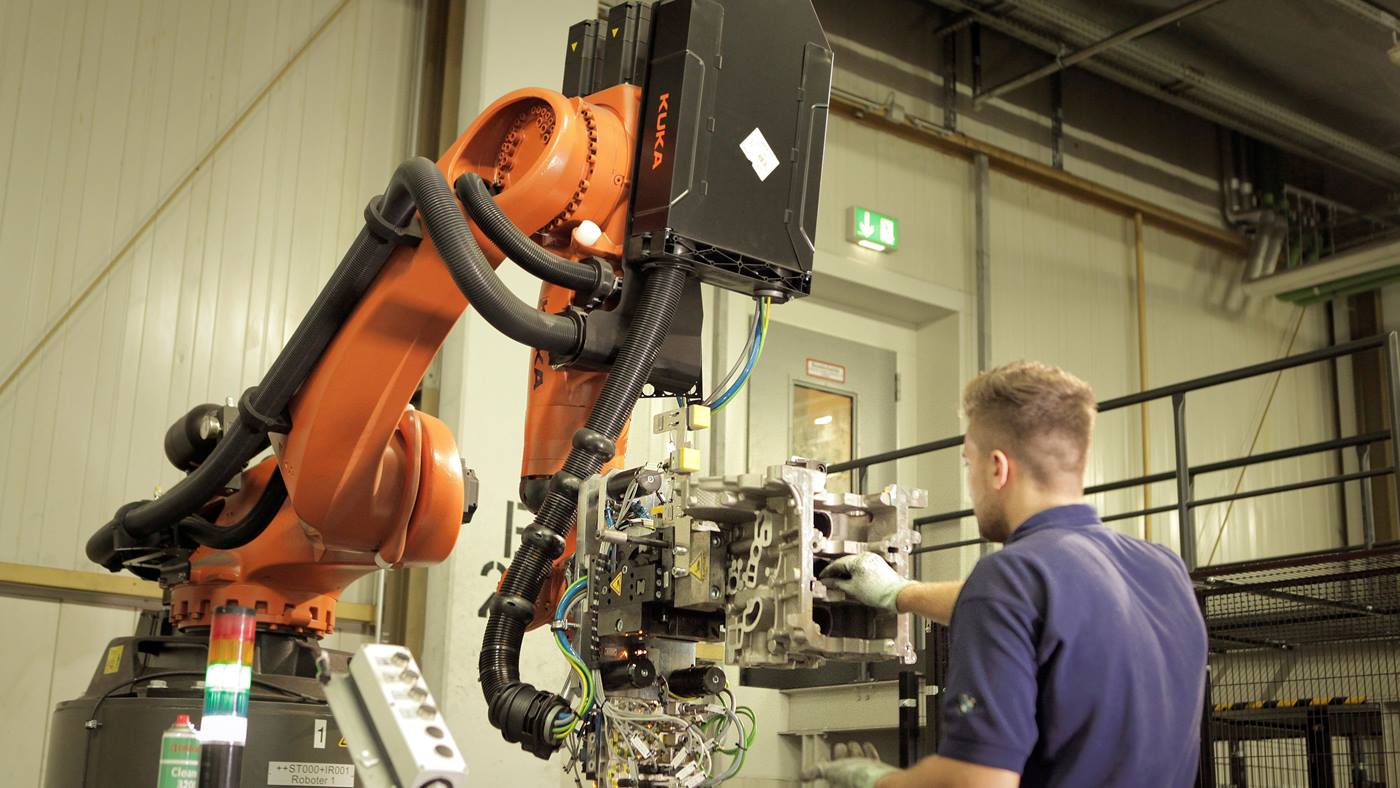
Die Rückmeldungen waren durchweg positiv. Die Taktzeiten können eingehalten werden und die Arbeit ist für die Mitarbeiter nun deutlich angenehmer.
Ausbau der bestehenden Anlage geplant
Die beiden Anlagen sind seit dem Jahr 2015 erfolgreich in Betrieb. Mittlerweile arbeiten Mohre und seine Kollegen an einer Erweiterung der Anlage. So sollen zukünftig zwei weitere Prüfstände für die Qualitätssicherung errichtet werden.
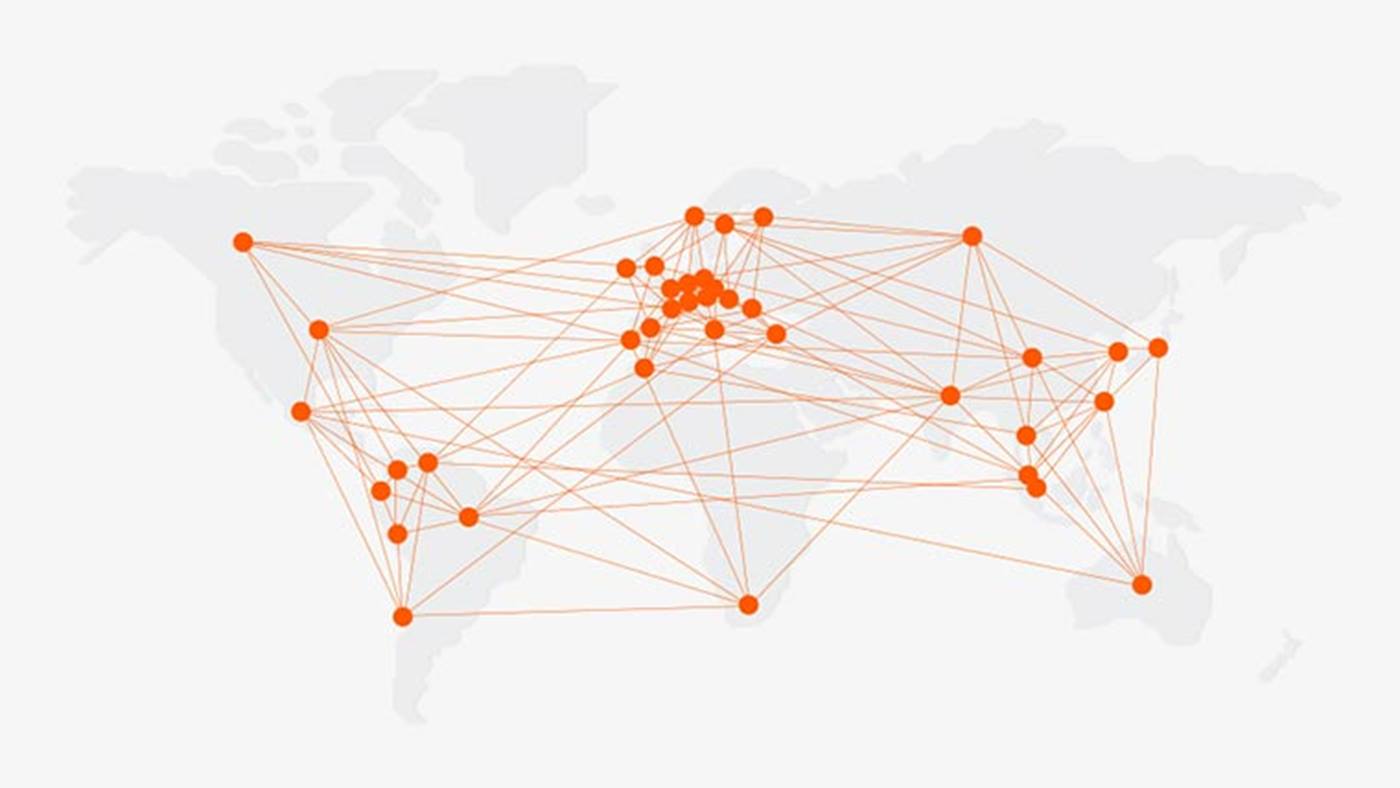